La maintenance prédictive est devenue un mot à la mode dans l’industrie au cours des dernières décennies, alors que les usines tentent de réduire leur coût total de possession (TCO : Total Cost of Ownership) en prévenant les pannes et les temps d’arrêt « juste à temps ». Beaucoup supposent à tort que la mise en œuvre d’une stratégie de maintenance prédictive implique une refonte complète des opérations, mais en réalité, prendre quelques petites mesures peut faire une grande différence pour la disponibilité de la machine et l’OEE (overall equipment effectiveness : efficacité globale de l’équipement). Pour réussir, il est conseillé de s’engager avec un partenaire technologique de confiance. Pour SMC, un leader mondial des solutions de contrôle pneumatique, le « P » de la maintenance prédictive devrait être synonyme de « progrès » et non de « peine ».
Par Oliver Prang, Expert Développement Business Digital, SMC Allemagne
DECEMBRE 2021
Selon un rapport d’IndustryWeek, les temps d’arrêt non-planifiés coûtent aux fabricants industriels environ 50 milliards de dollars par an. La défaillance de l’équipement est à l’origine de 42 % de ces temps d’arrêt imprévus. Personne ne peut donc contester la nécessité d’un régime d’entretien efficace.
Différentes stratégies
Il existe de nombreux types de maintenance : réactive, préventive et prédictive, sans doute la plus courante. Mais comment donner un sens à ces termes apparemment disparates ? Certains suggèrent que l’utilisation de la santé humaine constitue une analogie appropriée avec la santé de la machine. Prenez le diabète, par exemple, une maladie qui touche actuellement 422 millions de personnes dans le monde, selon l’Organisation Mondiale de la Santé.
L’utilisation de la maintenance réactive dans ce sens serait après qu’un médecin ait confirmé le diabète d’un patient. Le patient se concentrera ensuite sur la prise d’injections ou de comprimés pour contrôler la glycémie, parallèlement à un régime alimentaire contrôlé qui réduit ou même évite la consommation de sucre et de glucides. En revanche, l’application d’une maintenance préventive reviendrait à traiter la maladie sans aucun symptôme. Le patient continue ensuite à maintenir un mode de vie sain, soutenu par un régime alimentaire contrôlé et un plan d’exercice pour, espérons-le, éviter tout risque de développer un diabète. La maintenance prédictive, c’est quand quelqu’un est peut-être « pré-diabétique », mais toujours dans une limite sûre ou avec des critères acceptables. La surveillance régulière de la glycémie et de l’IMC (indice de masse corporelle), par exemple, révélera si la situation est stable ou se détériore au fil du temps et aidera à déterminer si / quand d’autres interventions sont nécessaires.
Les ingénieurs de production veulent augmenter la fiabilité des machines en minimisant la possibilité de temps d’arrêt coûteux et perturbateurs. Dans de nombreux cas, cela implique de mélanger diverses stratégies de maintenance dans différents scénarios de production, plutôt que de sélectionner celle qui est tendance sur les médias sociaux. Il y a de nombreux facteurs à prendre en compte ici, notamment le coût de la mise en œuvre et de la gestion par rapport au nombre d’instances de temps d’arrêt.
Les données sont reines
Le mot clé n’est même pas prédictif ou préventif, mais les données. La mise en œuvre d’un programme de maintenance prédictive nécessite trois éléments de base : les données, le temps et l’analyse. La donnée est un allié pour prendre de l’avance - la version moderne d’une boule de cristal - et augmenter la fiabilité de la machine. Une connaissance approfondie des raisons pour lesquelles un actif commence à échouer. C’est précisément pour cette raison que le partenariat avec un spécialiste de l’automatisation réputé peut rapporter des dividendes importants.
D’un point de vue pratique, la règle numéro un est de garder les choses simples. SMC soutient ses clients avec une approche « une partie à la fois », allant de l’analyse des fuites d’actionneurs, par exemple, à l’analyse partielle de la machine et à l’analyse de la machine entière. Ainsi, toutes les connaissances, les définitions de processus et les responsabilités du personnel passent d’un petit projet initial à un plus grand de la manière la plus fluide possible.
Un bon exemple est un vérin pneumatique : le cheval de bataille de nombreuses machines industrielles. Parmi les modes de défaillance courants pour les actionneurs pneumatiques, il y a un joint de piston qui fuit. Ces défauts peuvent être difficiles à détecter, entraînant une perte de pression. Une perte de pression de fonctionnement de seulement 0,1 MPa peut affecter négativement la puissance théorique d’un vérin (piston de 32 mm d’alésage) de 17%. Un autre effet secondaire d’un joint défectueux est une augmentation de la consommation d’air afin de compenser la fuite.
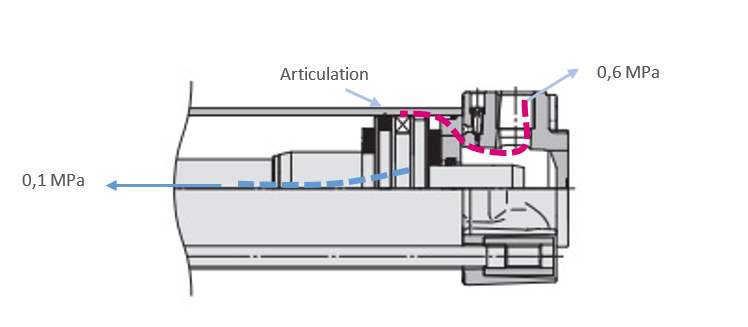
Résultat théorique [N]
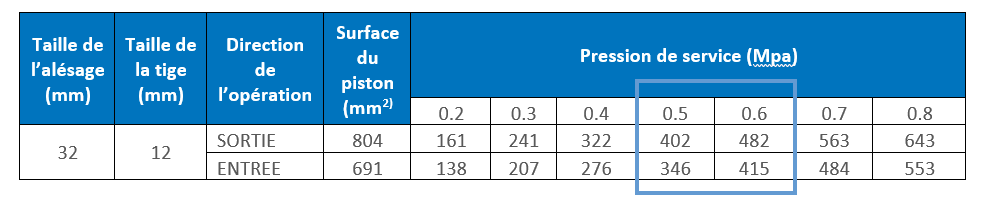
Extraction des tableaux du catalogue CP96 de SMC
Ici, l’adoption d’une stratégie de maintenance prédictive n’implique guère plus que l’installation d’un capteur de pression sur chaque canal de vérin et la surveillance de la pression dans le temps. Tous les défauts du joint deviendront rapidement apparents en raison de courbes de performance anormales par rapport à celles « apprises » pour un fonctionnement normal. Grâce à l’apprentissage automatique et à l’analyse en temps réel, il est possible de mettre en œuvre une maintenance prédictive en temps opportun avant d’encourir des pertes de performances ou des temps d’arrêt majeurs.
En plus des capteurs de pression, d’autres capteurs clés peuvent inclure des capteurs à induction pour calculer la vitesse du vérin et aider à détecter les niveaux de contamination sur les guides, par exemple. L’installation d’un réseau de capteurs de débit pour suivre en permanence l’utilisation de l’air comprimé (et toute fuite ou dysfonctionnement) sur le circuit pneumatique est une autre recommandation.
Une intelligence réelle
Bien sûr, toute l’intelligence n’est pas nécessairement artificielle. Effectivement, les machines peuvent apprendre, prédire et prévenir, mais elles ont toujours besoin d’une intervention humaine pour définir des variables appropriées à surveiller et fixer des limites acceptables / inacceptables. En outre, les humains doivent sélectionner les composants de la machine à adapter aux capteurs, car tous ne seront pas essentiels à la disponibilité et à la productivité. Les budgets, le temps et la disponibilité du personnel entrent également dans l’équation.
Avec ces pensées à l’esprit, s’associer à un spécialiste de la technologie éprouvé est une stratégie prudente. Par exemple, la mise en commun des connaissances de SMC sur les composants d’automatisation avec la connaissance individuelle des machines d’un client constitue une combinaison puissante et ingénieuse.
Un autre facteur potentiel ici concerne la maintenance basée sur la fiabilité. Concevoir dès l’origine signifie identifier les réductions des coûts de maintenance inutiles sur la base de l’AMDEC (Analyse des Mode de Défaillance, de leur Effets et de leur Criticité). Cette approche se concentre essentiellement sur les différents échecs qui pourraient survenir et leurs conséquences potentielles. SMC facilite cette tâche en mettant à disposition des outils de configuration sur son site Web pour les équipements pneumatiques, les collecteurs de soupapes et les vérins, contribuant à optimiser la sélection de produits – et les performances – pour l’application en cours.
En fin de compte, beaucoup supposent que la maintenance prédictive est la solution ultime pour réduire les temps d’arrêt et améliorer l’OEE. Pour l’instant, ce n’est pas le cas, même si la situation pourrait bien évoluer dans les années à venir en raison d’un nombre croissant d’initiatives intelligentes dans les usines du monde entier. D’ici là, rassembler les connaissances est la clé. En tant que partenaire, SMC est à la hauteur du défi.