En las últimas décadas, el mantenimiento predictivo se ha convertido en una palabra de moda en el sector, ya que las fábricas intentan reducir el coste total de propiedad de sus bienes de equipo previniendo los fallos y los tiempos de inactividad "justo a tiempo". Muchos asumen erróneamente que implantar una estrategia de mantenimiento predictivo implica una revisión completa de las operaciones, pero en realidad, dar unos pequeños pasos puede suponer una gran diferencia en el tiempo de actividad de las máquinas y en la OEE (eficacia general de los equipos). Para garantizar el éxito, es aconsejable contar con un socio tecnológico de confianza. Para SMC, líder mundial en soluciones de control neumático, la "P" de mantenimiento predictivo debe significar "progreso", no "dolor".
Por Oliver Prang, Experto en Desarrollo de Negocio Digital, SMC Alemania
DICIEMBRE 2021
Según un informe de IndustryWeek, los tiempos de inactividad imprevistos cuestan a los fabricantes industriales unos 50.000 millones de dólares al año. Las averías de los equipos están detrás del 42% de este tiempo de inactividad imprevisto. Por tanto, nadie puede cuestionar la necesidad de un régimen de mantenimiento eficaz.
Diferentes estrategias
Existen muchos tipos de mantenimiento: reactivo, preventivo y predictivo son los más comunes. Pero, ¿cómo dar sentido a estos términos aparentemente dispares? Algunos sugieren que la salud humana es una analogía adecuada de la salud de las máquinas. Tomemos como ejemplo la diabetes, una enfermedad que afecta actualmente a 422 millones de personas en todo el mundo, según la Organización Mundial de la Salud.
Utilizar el mantenimiento reactivo en este sentido sería después de que un médico haya confirmado la diabetes de un paciente. Posteriormente, el paciente se centrará en tomar inyecciones o pastillas para controlar los niveles de glucosa en sangre, junto con una dieta controlada que reduzca o incluso evite la ingesta de azúcar y carbohidratos. En completo contraste, aplicar un mantenimiento preventivo consistiría en tratar la enfermedad sin ningún síntoma. El paciente sigue manteniendo un estilo de vida saludable, con el apoyo de un plan controlado de alimentación y ejercicio, para evitar el riesgo de desarrollar diabetes. El mantenimiento predictivo es cuando alguien es quizá "prediabético", pero sigue dentro de un límite seguro o de unos criterios aceptables. El control periódico de la glucosa en sangre y del IMC (índice de masa corporal), por ejemplo, revelará si la situación se mantiene estable o se deteriora con el paso del tiempo y ayudará a determinar si es necesario realizar más intervenciones y cuándo.
Los ingenieros de producción quieren aumentar la fiabilidad de las máquinas reduciendo al mínimo la posibilidad de paradas costosas y perjudiciales. En muchos casos, esto implica mezclar varias estrategias de mantenimiento en diferentes escenarios de producción, en lugar de seleccionar la que está de moda en las redes sociales. Hay muchos factores a tener en cuenta, como el coste de implantación y gestión en comparación con el número de paradas.
El dato es el rey
La palabra clave ni siquiera es predictivo o preventivo, sino datos. Implantar un programa de mantenimiento predictivo requiere tres cosas básicas: datos, tiempo y análisis. Los datos son un aliado para adelantarse al tiempo -la versión moderna de una bola de cristal- y aumentar la fiabilidad de las máquinas. Se necesita un amplio conocimiento de por qué un activo está empezando a fallar. Precisamente por este motivo, asociarse con un especialista en automatización de renombre puede reportar importantes dividendos.
Desde un punto de vista práctico, la regla número uno es simplificar las cosas. SMC ayuda a sus clientes con un enfoque de "una pieza a la vez", que va desde el análisis de fugas de actuadores, por ejemplo, hasta el análisis parcial de la máquina y el análisis de la máquina completa. De este modo, todos los conocimientos, definiciones de procesos y responsabilidades del personal se transfieren de un pequeño proyecto inicial a otro mayor de la forma más sencilla posible.
Un buen ejemplo es un cilindro neumático: el caballo de batalla de muchas máquinas industriales. Entre los fallos más comunes de los actuadores neumáticos está la fuga de la junta del pistón. Estos defectos pueden ser difíciles de detectar y provocar una pérdida de presión. Una pérdida de presión de funcionamiento de sólo 0,1 MPa puede afectar negativamente a la fuerza teórica de salida de un cilindro (pistón de 32 mm de diámetro) en un 17%. Otro efecto secundario de una junta defectuosa es un aumento del consumo de aire para compensar la fuga.
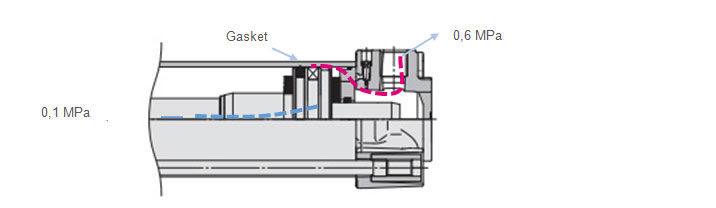
Esfuerzo teórico [N]

Gráficos extraídos del catálogo CP96 de SMC
En este caso, adoptar una estrategia de mantenimiento predictivo supone poco más que instalar un sensor de presión en cada canal del cilindro y controlar la presión en función del tiempo. Cualquier defecto en la junta pronto se hará evidente debido a curvas de rendimiento anormales en comparación con las "aprendidas" para un funcionamiento normal. Con el aprendizaje automático y el análisis en tiempo real, es posible aplicar a tiempo el mantenimiento predictivo antes de incurrir en pérdidas de rendimiento o tiempos de inactividad importantes.
Además de los sensores de presión, otros sensores clave podrían incluir sensores de inducción para calcular la velocidad del cilindro y ayudar a detectar niveles de contaminación en las guías, por ejemplo. Otra recomendación es instalar una red de sensores de caudal para controlar continuamente el uso de aire comprimido (y cualquier fuga o avería) en el circuito neumático.
Inteligencia real
Por supuesto, no toda inteligencia es necesariamente artificial. Por supuesto, las máquinas pueden aprender, predecir y prevenir, pero siguen necesitando la intervención humana para definir las variables adecuadas que deben supervisarse y establecer los límites aceptables e inaceptables. Además, los humanos deben seleccionar qué componentes de la máquina equipar con sensores, ya que no todos serán críticos para el tiempo de actividad y la productividad. Los presupuestos, el tiempo y la disponibilidad de personal también entran en la ecuación.
Con estas ideas en mente, asociarse con un especialista en tecnología de probada eficacia es una estrategia prudente. Por ejemplo, unir los conocimientos de SMC sobre componentes de automatización con los conocimientos sobre máquinas individuales de un cliente constituye una combinación potente y llena de recursos.
Otro factor potencial es el mantenimiento basado en la fiabilidad. Diseñar desde el origen significa identificar reducciones en los costes innecesarios de mantenimiento basándose en el AMFE (análisis de los efectos de los modos de fallo). En esencia, este enfoque se centra en los distintos fallos que podrían producirse y sus posibles consecuencias. SMC facilita esta tarea alojando herramientas de configuración en su sitio web
Para líneas aéreas neumáticas, colectores de válvulas y cilindros, ayuda a optimizar la selección de productos -y el rendimiento- para la aplicación en cuestión.
En última instancia, muchos asumen que el mantenimiento predictivo es la solución definitiva para reducir el tiempo de inactividad y mejorar la OEE. Por ahora, no es así, aunque la situación podría evolucionar en los próximos años debido al creciente número de iniciativas inteligentes en fábricas de todo el mundo. Hasta entonces, aunar conocimientos es la clave. SMC, que trabaja en equipo, está preparada para el reto.