Dew point can be an overwhelming term, but put simply, it is the temperature at which water becomes visible. The water droplets that you can see in your cold drink derive from the dew point.
By Axel Delsaux, Product Marketing, SMC France
OCTOBER 2021
Talking about dew point is essentially, talking about water vapour and moistness. Even though we do not see it, air contains water in a vapour (gas) form, and its amount is directly proportional to its temperature.
As air cools the water vapour within it condenses and changes from a vapour to a liquid, reaching the temperature where the air becomes saturated; this is called the dew point. If the temperature drops, additional moisture will form into tiny droplets or condensation. Natural examples of atmospheric dew point (ADP°C) can be seen where warm air comes into contact with cold surfaces, as in our example before.
The term atmospheric dew point is most relevant to weather conditions. In compressed air installations and pneumatic systems, pressure dew point is more appropriate.
Pressure dew point (PDP °C) is the temperature at which condensation occurs at elevated pressure; typically, 7 bar is used as this is the most common Compressed Air System (CAS) pressure.
To sum up, as the temperature can drop along your CA, leading to water condensation, you need to keep an eye on the dew point.
Removing condensed water is not the same as removing moisture
Addressing the dew point is addressing moistness. Moistness appears when there is a drop in temperature along your production line. As we want to avoid the potential of having water droplets going around our CAS, we address dew point.
Why is it important to be managed?
Moisture, in general, can lead to corrosion, blockages in pipes, machinery breakdowns, swelling of seals causing additional friction, contamination and freezing. Furthermore, moisture can be especially harmful to water sensitive processes such as spray painting or those that could be contaminated with water as is the case in the pharmaceutical industry.
The question - how sensitive is your equipment and process to water droplets? - is what you need to answer.
There are two main steps to address the moisture in your airline.
How to address the moisture in the first instance?
Simple. By installing a refrigerated air dryer at a controlled point in the CAS, normally after the compressor or the air tank. This solution dries the air by cooling it. The compressed air passes through the heat exchanger and its temperature is lowered to 3 ºC forcing the vapor contained in the air to condense. The water that forms into a liquid is easy to remove via the dyer’s drain, therefore ensuring that the air that enters your production process is drier.
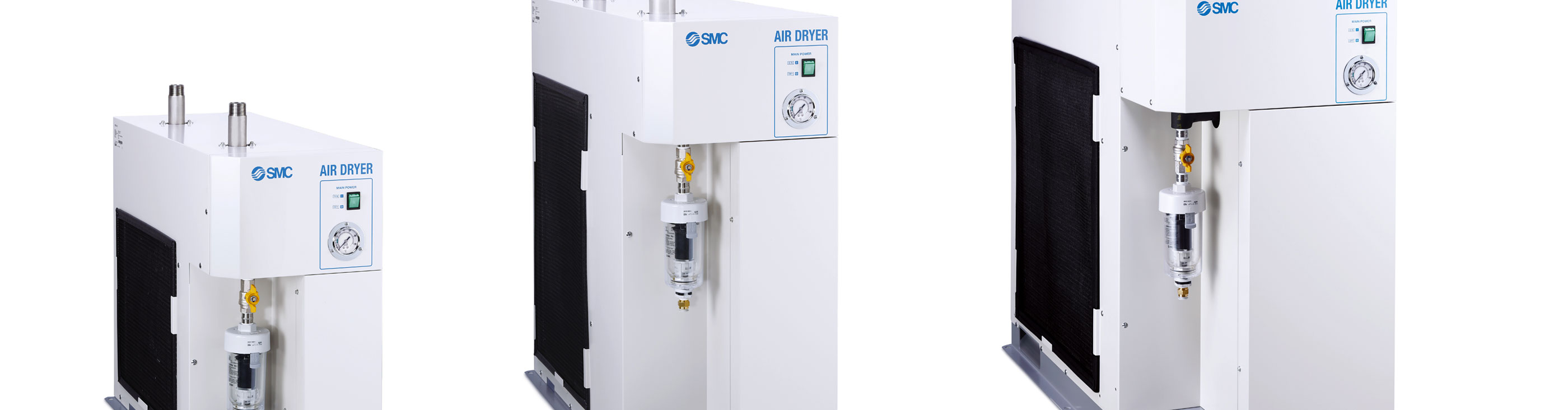
SMC´s Refrigerated Air Dryers - IDFA Series – come with standard stainless steel heat exchanger, which ensures a long-life, cool compressed air output and anti-corrosive treatment for copper tube as some of its options
Optimised management of the dew point – The membrane air dryer
When there is an application that requires an atmospheric pressure dew point that is much lower (from -20 ºC to -60 ºC) such as the one required for example in semiconductor manufacturing or in fine particle drying, our recommendation is to install membrane dryers to remove moistness only where necessary. The membrane air dryer uses hollow fibres composed of a macro molecular membrane through which moisture passes easily but is difficult for air (oxygen and nitrogen) to pass through. A membrane air dryer is a cost-effective solution for point-of-use applications ideal for example in pharmaceutical manufacturing, packaging, and laboratory environments.
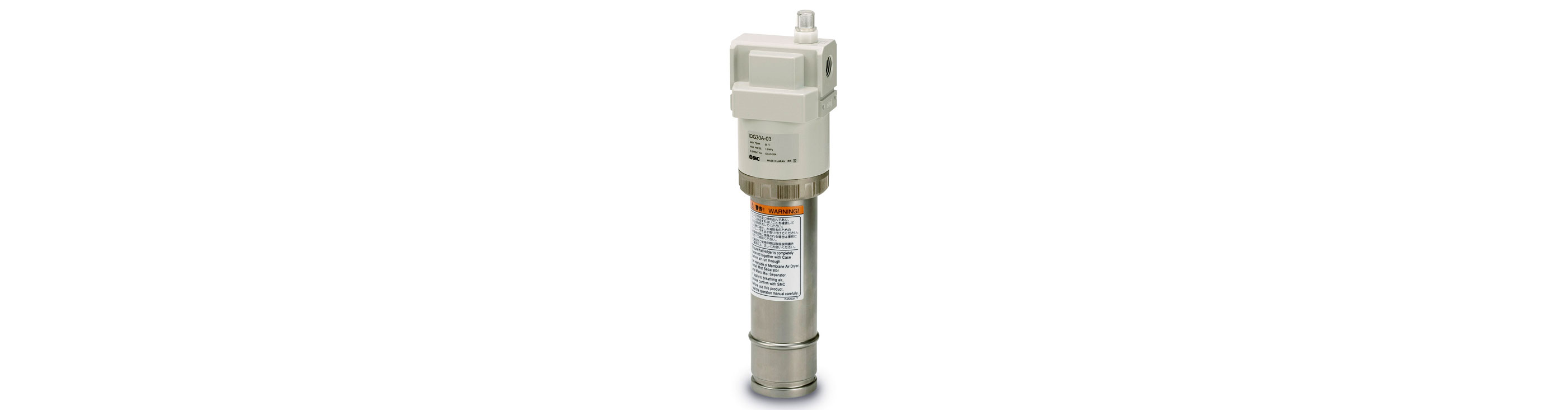
SMC´s Membrane Air Dryer, IDG-A Series. Compact solution with no electrical consumption.
The importance of the dew point depends on the intended usage of the compressed air, and defining the appropriate air dryness and the correct solution widely depends on your specific needs. Simply contact your SMC local Expert to guide you in the best and most efficient air drying solution for your application.