A plug-and-run solution consisting of powerful compressed air components from SMC realises modularised and industrialised helium leak testing systems from Bosch Manufacturing Solutions.
Oliver Meyer (SMC Germany), Valentino Nadale (Bosch Manufacturing Solutions) and Andreas Schmid (SMC Germany) are delighted with the successful joint project. (Source: SMC Deutschland GmbH)
The be-all and end-all for the safe and reliable use of components is their tested quality. They include products that must successfully pass a leak test before they are allowed to leave a factory. Such requirements are placed on e-machines and fuel cells, for example – in the case of the latter, the requirements are particularly high, and testing must be carried out after various assembly steps. Reliable and efficient operation of leak testing systems therefore requires suitable pneumatic components such as valves and filters/controllers, as well as connecting parts such as hoses, fittings and process valves. A successful joint project between SMC and Bosch Manufacturing Solutions shows how high requirements and ideal coordination can be realised from a single source.
High product quality is a top priority across all industries – both in terms of the company's own portfolio and the quality assurance solutions used. This is all the more important when it comes to components that have to fulfil the highest standards in terms of safety and reliability. They include fuel cells, which play an important role in the generation of clean and climate-neutral energy. Before they can be installed in lorries, for example, they undergo various assembly steps, during which leak tests are subsequently required for quality assurance. Various requirements relating to leakages and sizes make the tests a real challenge.
This is something that Bosch Manufacturing Solutions also constantly has to master: The wholly owned subsidiary of Robert Bosch GmbH is a global supplier in the field of special machine construction for both the Bosch Group and external customers. Headquartered in Stuttgart, the company has nine locations worldwide and generates annual sales of around 500 million euros. With around 1700 employees, it offers customised and intelligent assembly and testing solutions throughout the entire product life cycle, including advanced manufacturing processes and technologies, as well as digital and intelligent solutions and services.
Bosch Manufacturing Solutions relies on the automation specialist SMC for the pneumatic components required in the area of fuel cell production for systems for leak testing – in the areas of intermediate testing and end-of-line testing – as well as in development and prototyping.
Comprehensive requirements profile required
The particularly high demands of the project were the dimensions of the 10m3 test chamber and the aim of modularising and industrialising the accumulation test carried out with it. This therefore enables mobile fuel cells for lorries, for example, and stationary SOFC fuel cells for buildings and other things, to be tested. In addition, the leakages are not calculated using the evaluation technology supplied with the mass spectrometer, but using a separate algorithm that is applied to the raw sensor data during the accumulation period. Helium was intended as the test medium, which is why the SMC components had to be suitable for this purpose as well.
"The high standardised requirements – especially for fuel cell production lines – prompted us to find SMC as a partner for standardised solutions," says Valentino Nadale, Senior Manager Leakage Testing at Bosch Manufacturing Solutions. "They include high pressures of up to 207 bar and a very high tightness of up to 10-6 mbar/l per second. The various components of the solution should also be available from a single source and be plug-and-run-ready as a complete system. "The compactness factor is also important to us for optimising the installation space. The panel pressurises the test specimen with helium or nitrogen in addition to oxygen for flushing and then to confine it. Meanwhile, various sensors on the panel monitor the individual processes such as differential pressure, helium concentration, flow rate and pressure."
An optimally harmonised solution
In constructive consultation between SMC and Bosch Manufacturing Solutions, in addition to the basic technical requirements, the possibilities for outsourcing design and production to SMC were determined and ultimately planned. AP Tech valves, the JSY valve terminal, SRH clean room controllers, SRP precision controllers and other standard products from SMC provided the solutions for this.
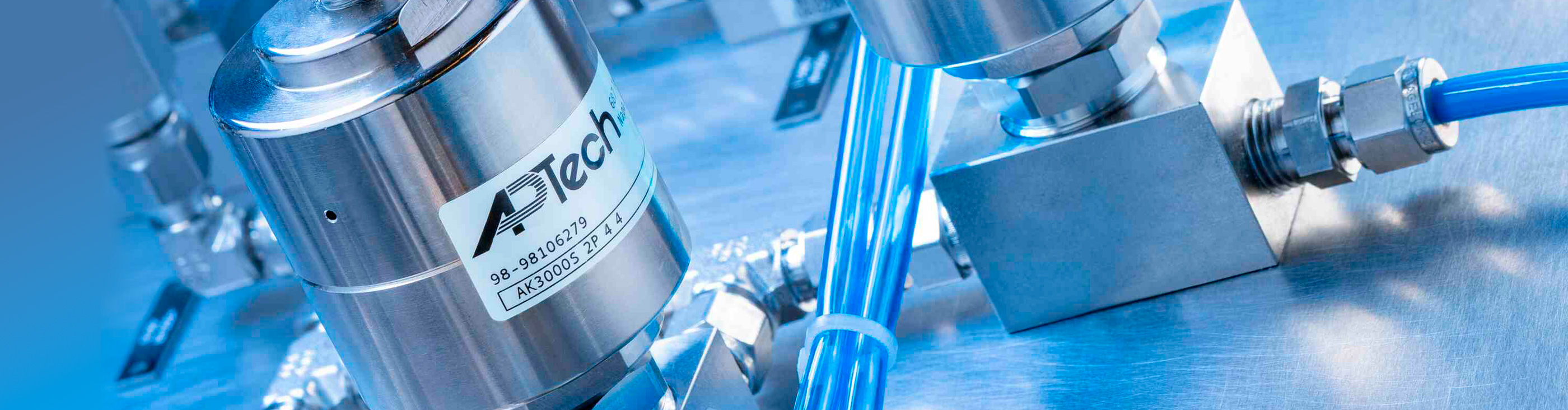
"The biggest challenge for us was that the first projects we realised consisted exclusively of individual custom-made products manufactured as single units," says Andreas Schmid, Sales Engineer Robert Bosch at SMC Germany, adding: "This meant we had to redesign from scratch again and again. In addition to our technical expertise, we were also able to incorporate a great deal of experience from past projects for testing diesel pump technology test applications into the current developments – and ultimately offer Bosch Manufacturing Solutions ready-made plug-and-run solutions for accumulation testing of fuel cells."
Reliable leak testing for long-range fuel cells
Previously, Bosch Manufacturing Solutions had assembled test panels itself from components from various manufacturers. The new approach simplifies the entire process, with SMC supplying everything from a single source and fully assembled. "The excellent cooperation between our teams and the SMC teams played a decisive role in realising our requirements in terms of outsourcing design and production," says Valentino Nadale. "Thanks to the compact design of the individual components, we can save between 10 and 15 per cent of installation space per panel.With 5 to 6 panels in a single production line, that makes a noticeable difference. The fast delivery was a particularly positive surprise, especially given the current difficult supply chain conditions."
"The reliability of the fuel cells, which had a range of 800 km in test trucks, demonstrated, among other things, just how much the strengths of our plug-and-run solutions and SMC's many years of expertise pay off," emphasises SMC expert Andreas Schmid. "We see great potential for future projects with our JSX series valves, the PF3A flow sensors with temperature monitoring and our various electric drives, for example. We are looking forward to initiating further projects together with our colleagues from Bosch Manufacturing Solutions and developing new, exciting and successful concepts."