A rebirth in the name of innovation
The Turin-based company DMC Automation, creates a robotic island equipped with SMC components, including the innovative wireless fieldbus system. Both companies portray a solid and stimulating technological partnership oriented towards the search for cutting-edge solutions.
DMC Automation is a small-to-medium-sized company that boasts solid roots and a natural openness towards innovation. The company was founded in 1972 by Domenico De Caroli. In 1992 it began producing machines for the assembly of the metal structure that is in fact the 'skeleton' of car seats: this was a turning point for DMC as it marked the entry into a fundamental sector that is still one of the company's core businesses today.
All the biggest car seat manufacturers use machines supplied by the Turin-based company to make the internal structure of the seat. "We are specialized in machines for the assembly of this 'skeleton' starting from elements that are assembled together to realize the supporting structure of the seat, an important piece as it is linked to safety criteria" explains Carlo Amicilia, sales director of DMC Automation.
Simplify production
Accelerating and simplifying the production process using intelligent technologies is the philosophy with which DMC Automation approaches the market. "We want to work in the field of robotics and automation and for that we count with an in-house design and manufacturing office.
Everything we design is always pre-assembled and tested in-house before delivering it to our customer," explains Amicilia. "Our production program is quite articulated: machines and assembly lines for the car seats metal structures and also robotized assembly and welding lines. As well we develop machines and lines for, vision systems, material handling, testing equipment and above all machines and lines made to meet the individual needs of our customers" explains the manager.
An important partnership
In order to meet the needs of its customers in a precise and timely manner, DMC relies on the support of leading partners. Thanks to its expertise and constant technological innovation, the Turin-based company is able to respond to customers' requests but also to expand its field of action and approach new market niches. "SMC is a must for us, a fundamental partner and we consider their components a real standard, which facilitates us the design and allows us to have a continuity of service, spare parts, product updates and much more" underlines Amicilia. "There is the certainty of the quality of their components, but we are also very satisfied with the close collaboration with their team of technicians and salespeople, with whom a real technological partnership has developed over time in both pre and post sales. This has led us to the use of new and cutting-edge products in terms of technological innovation, which is an important plus for our customers" he adds.
An innovative robotic island
Among the machines produced in the DMC plant in Grugliasco stands out a robotized island equipped with SMC components, characterized by a control transmission system realized through wi-fi, a decidedly avant-garde innovation for the sector. Intended for a Turkish customer, it is a jewel in terms of innovation. "It is an automatic machine for the assembly and testing of a car's rear backrest locking system. It features manual loading stations with presence controls via cameras while all the assembly stations are automatic. There is also a robot for the 'transfer' from a first table to the testing table. Parts are marked and values stored on a PC for traceability. On this machine we decided to use the wireless fieldbus system that allows us to have the I/Os on board the table without the use of the classic air-electric joint, which is subject to wear and tear, is not easy to maintain and requires a dedicated electrical cabinet that involves additional costs," explains Carmelo Todaro, Technical Office Manager. The heart of the machine consists of a series of electrical connections that are in contact via wi-fi with the central detector, which is able to manage them without contact. From phase to phase the table rotates and consequently all the groups rotate while the central pin remains fixed: every single element is therefore managed in wi-fi through SMC's innovative EX600W.
Effective solutions
"Many of our machines, including this robotic island, are made with rotary tables with different positions that transfer groups, subgroups or components from one workstation to another.
One of the problems is the need to maintain control during movement: when moving, the table should carry electrical wires and controls. The jump on wi-fi that SMC proposed to us was really enlightening and allowed us to solve this problem effectively," Carmelo Todaro points out.
The technological collaboration with SMC is full of new and innovative solutions. "The SMC flow switch is useful for troubleshooting and monitoring the air consumption in the plant and thus evaluating energy savings. In another application, we used the SMC CKZT series, which allowed us to clamp the entire diameter of the tube so to work evenly.
We have as well installed SMC´s electric actuators, especially the LEY series, which allows us flexibility in positioning and setting up the machine both to us during the pointing phase and to the customer in the various phases of process and part modification" concludes Todaro.
Integration 4.0
A final note: all DMC machines are already designed to meet the requirements of Industry 4.0, an important plus for companies that are already oriented to a production management with sophisticated systems. "For us it is fundamental to rethink and develop new production, organizational and management processes”.
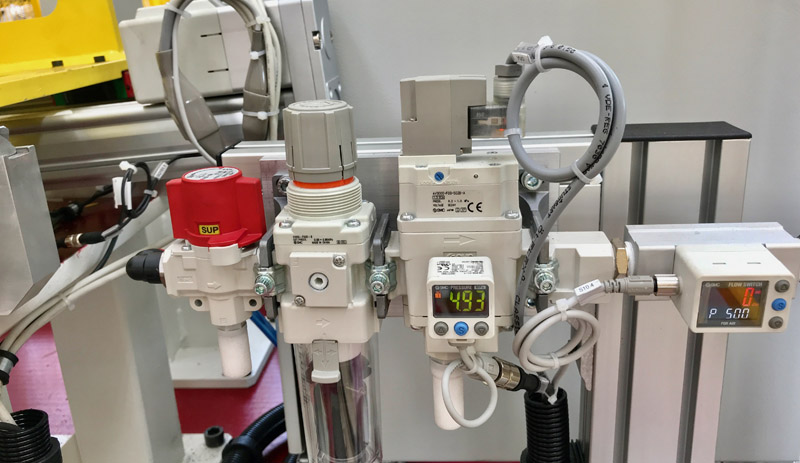
DMC Automation has long been working actively with SMC, the world leader in pneumatic automation. In the picture, the SMC flow switch mounted in a DMC machine.
Published in Technè (Open Factory) October 2019, Italia, written by Simona Recanatini
21. jun. 2021