Although most pneumatic machinery and equipment operates at 7 bar, I know from experience that taking steps to reduce the system’s operating pressure to 4 bar can enhance energy efficiency, cost savings and environmental credentials. After all, every company is usually looking to save something, be it money, air, CO2, or even the planet. Unfortunately, in the majority of cases, big savings do not happen overnight. Only by implementing small improvements step-by-step is it possible to bring about the overall gains desired. Here at SMC we have a simple yet highly effective product that can be one of those steps.
By Marek Strojil, Customised services, SMC Czech Republic
Our ZHV air amplifier multiplies air blow/suction by 4 and 3 times respectively. The upshot is that you can save up to 70% in air consumption through the ability to reduce input pressure, without any compromise in results. In fact, the ZHV outperforms alternative products from other suppliers in Europe, typically by around 20%.
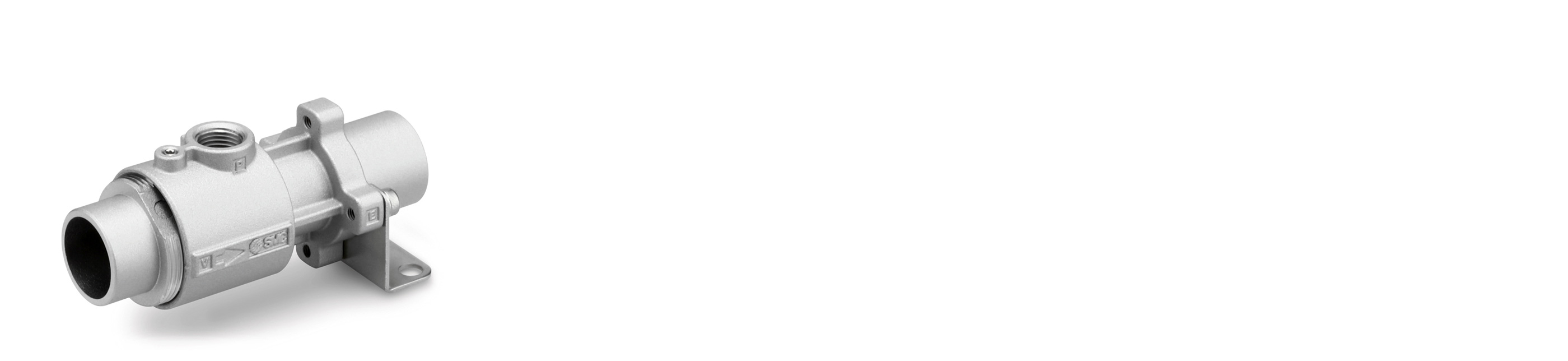
SMC´s Air Amplifier - Blow your air consumption away
An air amplifier has many uses, such as blowing away machining chips and water droplets. In suction applications, the device can collect dust/powder when performing resin part marking, and transfer or relocate loose items such as pellets in material handling tasks. Our ZHV is maintenance-free, easy-to-use and safe.
Importantly, an air amplifier can provide the solution to a number of your every-day workshop challenges, such as where an existing device has insufficient blow, where high air consumption is proving costly, or where air flow is too slow. In instances such as these, I’m well aware of the temptation to simply turn up the pressure, but this of course comes at a price. The reality is that a cost-effective alternative exists wherever you require a bigger output: an air amplifier. Although this solution is often not considered, it should be, because it can bring about notable savings.
In relation to their impact in reducing energy costs, you’ll be pleased to learn that air amplifiers are not expensive devices, as evidenced by a major brewery in Eastern Europe. The brewery’s bottling line was suffering from an inability to consistently adhere labels due to wet glass. However, by adopting our ZHV it was possibly to blow dry the bottles sufficiently to allow proper label adhesion. Along with a much-improved process, I can report that ROI (return on investment) was achieved in just 7½ months thanks to annual savings in air consumption. The brewery is also enjoying improved safety and simplified maintenance.
You’ll probably be aware that an alternative approach is to use a common air nozzle, which can sometimes be the right fit in applications where you require a high peak pressure. With an air amplifier, the output pressure is lower but the volume of air is higher to achieve a similar result. Most importantly of all, an air amplifier needs less pressure to achieve the same air flow, allowing you to reduce air consumption and enjoy the energy savings that come with generating less compressed air.
In all cases, the optimal way forward is to seek the advice of one of our specialists here at SMC.