SMC Customer case – Expertise in: Meeting your challenges
Detect every leak: Precise leak detection for technical components.
High-vacuum angle valves from SMC ensure clean and precise leak-detection tests at Worthmann
By Helmut Gerdes, Sales Engineer at SMC Deutschland
Whether for petrol or other substances: Liquid tank systems should always be absolutely leak-tight, otherwise things could become dangerous very fast. After manufacture, they are therefore tested thoroughly before being installed in vehicles. To this end, Worthmann has developed a helium leak-tightness test system, which uses high vacuum and mass spectrometers to identify even the smallest leaks in components – and it takes only one minute. High-vacuum angle valves from SMC’s XLA series provide the long service life and robustness necessary for the task.
Modern machines operate with a wide variety of substances – from lubricant oil and various fuels through to uric acid mixtures for the reduction of nitric oxide in car exhaust gases. For them to be transported to where they are needed, robust and above all, leak-tight, components are required. Because it can quickly become dangerous if fuel leaks from a car, for example, and drips onto a hot engine or electrical components. Worthmann provides a suitable solution with its leak-tightness testing systems: Thanks to a mass spectrometer, the system can detect even the smallest quantities of helium gas leakage in a high vacuum, and thus assesses a component for leak-tightness. To operate safely and precisely, the test system needs tough valves. Five high-vacuum angle valves from SMC’s XLA series quickly supply air and helium to where they are needed.
Worthmann Maschinenbau GmbH, based in Barßel-Harkebrügge near Oldenburg, has been developing and manufacturing sophisticated machinery since 1995 – ranging from machining and testing lines for fuel systems through to complete production lines. Thanks to Worthmann’s modern machine facilities, its 120 employees can also produce sophisticated individual assemblies. The company’s core competence is the design and construction of individual industrial facilities as well as complete production lines. Everything from a single source: From design, to production and assembly, right through to programming and commissioning for international customers. Another part of the Worthmann Maschinenbau Group is Maceas GmbH, which focuses on measurement and testing technology.
Checking everything is leak-tight
Everyone who has ever had a flat tire on a bicycle knows the principle of leak testing: The inner tube is inflated with air and held under water. The hole can be found where the air bubbles appear. However, particularly where modern tank systems are concerned, this type of test is insufficient. This is where automated leak-tightness testing systems come into play, which check every component for leaks quickly and with maximum accuracy.
These highly specialised systems use the inert gas helium. The test piece is placed in a vacuum chamber, and is evacuated, together with the chamber. Helium is then injected into the test piece as a test gas at overpressure. If there are any leaks, helium will escape and is pumped to a mass spectrometer, which counts the helium atoms. “And this is done extremely precisely, because the mass spectrometer can detect even single helium atoms. That is why the system has a threshold leak rate of 1.0 · 10-5 mbar · l/s,” stresses Steffen Akkermann, Project Manager at Worthmann. With the Worthmann system, up to 60 workpieces can be leak tested per hour.
Robust angle valves for high vacuum
To achieve this high throughput, the air has to be evacuated from the filler tube and test chamber quickly, in order to fill the test piece with test gas. In order to achieve the purest possible high vacuum, valves are needed that allow practically no gas through when closed, yet can be operated very quickly and frequently. “Furthermore, at high flow rates, ice crystals can form at deflection points on the angle valves, thus falsifying the test result by depositing test gas in the valves,” explains Christian Suchalla, Sales Engineer at SMC Deutschland. High-vacuum angle valves from SMC’s XLA series present an efficient solution for this: Thanks to a heater, they can be heated up to 150 degrees Celsius, thereby effectively preventing ice from forming at the deflection points. “The element is easily attached to the outside of the angle valve, and then heats the entire aluminium housing evenly,” says Christian Suchalla.
Angle valves are used at several important points in the leak-tightness testing system: They conduct air and test gas in and out of the test chamber, as well as the workpiece, and serve as a connection to the mass spectrometer. Christian Suchalla: “The valves are fitted with bellows and remain closed until pressurised.” They practically don’t outgas at all, which speeds up the evacuation of the test chamber and the workpiece enormously. In addition, a pump with a lower capacity can be used – this increases the efficiency of the entire system. Furthermore, the new XLA series angle valves are very durable: they are guaranteed to withstand up to 2 million cycles. Moreover, the bellows and the pneumatic actuator can be replaced separately on each individual valve. This saves on maintenance costs, because the whole valve doesn’t need to be replaced. At the same time, the modular set-up significantly reduces maintenance outlay.
Pure vacuum, thanks to strong angle valves
With the XLA high-vacuum angle valves from SMC, Worthmann’s leak-tightness testing system offers a fast, powerful solution for filler pipe production. “A further increase in efficiency is conceivable in future, by controlling the angle valves via our modular valve terminal, the SY3000,” says Christian Suchalla. Other applications for the robust XLA valves are, for example, vacuum freeze-drying systems in the food industry, aluminium coating systems for vehicle headlights, or anywhere that the purest possible high vacuum is required.
Quotations from:
Christian Suchalla, Sales Engineer at SMC Germany
Steffen Akkermann, Project Manager at Worthmann
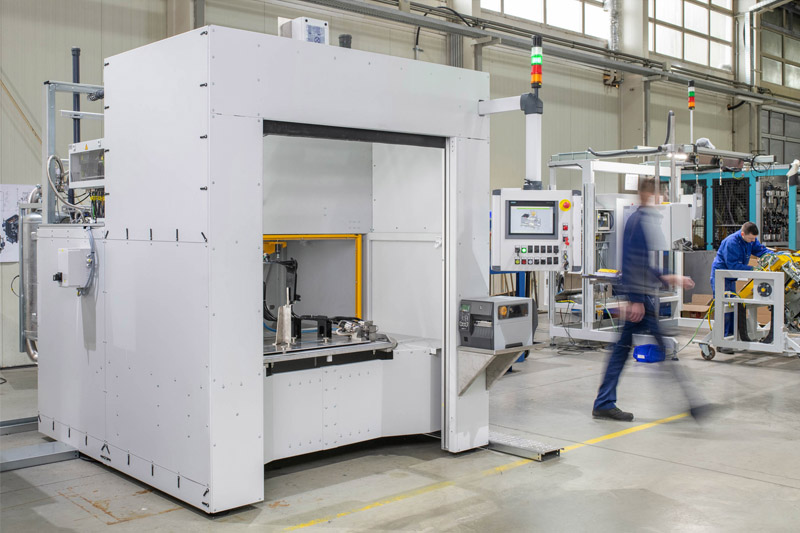
[Image 1] Detect any leaks: The leak-tightness testing system from Worthmann Maschinenbau GmbH quickly and reliably detects leaks thanks to SMC’s XLA high-vacuum angle valves.
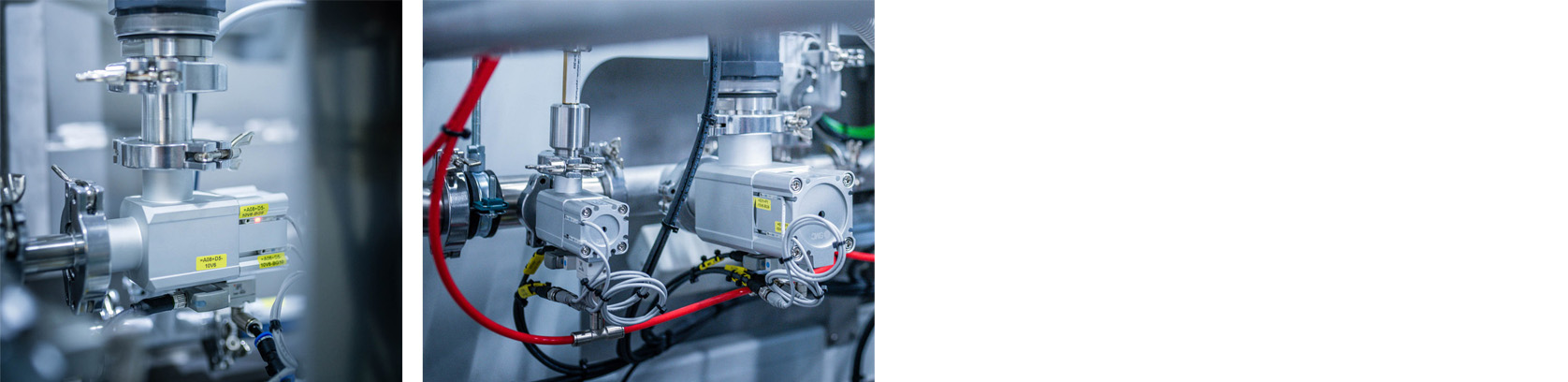
[Image 2 + 3] Think outside the box: The new angle valves from SMC’s XLA series have replaceable bellows seals and pneumatic actuators, which save time and money on maintenance, because there is no need to replace the entire valve.

[Image 4] In case it gets cold: Thanks to external heaters, the new high-vacuum angle valves in SMC’s XLA series prevent icing in operation, thereby ensuring particularly accurate test results.
17. pro 2020.