Por Danilo Giordana, Responsable de eficiencia energética, SMC Italia
Al entrar en el Informe Técnico ISO/TR 22165, que trata de la mejora de la eficiencia energética de los sistemas neumáticos, y leer la introducción, hallamos esta frase: " Solo si la máquina está óptimamente adaptada a las necesidades (por ejemplo, ciclo de trabajo, precisión, grado de automatización), puede aplicarse el concepto energético desarrollado para ella".
¿Qué significa "óptimamente adaptada"? Más allá de un diseño orientado a garantizar la una relación óptima entre la productividad y el consumo, podemos identificar tres vías para responder a esta pregunta.
1- El concepto de digitalización: la recopilación de datos a lo largo del tiempo para analizar el comportamiento de la máquina y compararlo con máquinas similares. Hoy en día, aunque se hable mucho sobre este tema, el estado actual del parque de máquinas está aún lejos de la digitalización total.
2- El mantenimiento basado en condiciones (CBM) que ayuda a mejorar la eficiencia funcional. Solo alcanzando las condiciones óptimas de funcionamiento de una máquina, también desde el punto de vista neumático, estableceremos una especie de "huella digital" de la máquina y conseguiremos detectar con rapidez cualquier desviación.
3- La maquinaria debe realizar su cometido de forma sostenible y eficiente desde el punto de vista energético, consumiendo solo lo mínimo y cuando se requiera.
Air Management System de SMC– AMS20/30/40/60 Series (Photo 1 & 2). En el display se muestran los parámetros en tiempo real: presión, caudal de aire instantáneo, valor de consumo de aire, temperatura del fluido
Analicemos ahora cómo responde a estos imperativos el Air Management System (AMS) de SMC (foto 1). En lo que respecta a los dos primeros aspectos, la digitalización y el CBM, el sistema recopila datos relativos a la presión, la temperatura, el caudal instantáneo, el consumo, las paradas de la máquina y las desviaciones debidas a fugas de aire, y lo transmite todo al ordenador de la planta configurado para recopilar y analizar datos. Los datos se envían a través de Ethernet-IP, Profinet, EtherCAT o el protocolo OPC UA (Open Platform Communications United Architecture). La unidad central del sistema, denominado unidad base, se conecta mediante un cable Ethernet al PLC o sistema de adquisición de datos, y puede actuar como pasarela Wireless de otras diez unidades remotas. La pantalla del dispositivo ya permite ver algunos parámetros clave en tiempo real (foto 2). Cada una de estas unidades incorpora un puerto IO-Link adicional que permite conectar un dispositivo extra.
Por otro lado, en cuanto al ahorro energético y la consiguiente reducción de emisiones de CO2, el sistema es capaz de reconocer cuándo la máquina está detenida. Después de un tiempo establecido por la ingeniería del proceso, el AMS pone la máquina en modo de “stand-by”, reduciendo la presión a un valor menor establecido, ahorrando así el aire consumido en posibles fugas del sistema. Cabe destacar que existe una correlación directa entre el nivel de presión y el valor de consumo de energía (fugas). Transcurrido un tiempo determinado, el sistema puede aislar completamente la máquina hasta el siguiente rearranque.
¿Qué hace que el AMS sea un sistema flexible?
El AMS incorpora la posibilidad de programar el sistema directamente a través de la función Web Server (foto 3). Conectando un ordenador portátil al dispositivo, es posible programar el umbral y establecer el tiempo para poner la maquinaria en modo “stand-by” y, si es necesario, para desconectarla completamente de la red neumática. Esta función facilita enormemente en producción la personalización del funcionamiento de la máquina y, por tanto, la reducción del consumo de energía. Los parámetros clave del dispositivo también se pueden programar fácilmente desde el teclado del equipo, por lo que las personas autorizadas siempre podrán cambiar fácilmente los ajustes. Al programar el AMS utilizando este método, no es necesario modificar el programa del PLC de la máquina; incluso una máquina con lógica de relés puede hacerse "inteligente" en lo que respecta al consumo de energía y la sostenibilidad.
Foto 4 - Gráfico de funcionamiento, los valores numéricos son ilustrativos
En cuanto a la instalación, el sistema debe colocarse a la entrada de la maquinaria o aplicación que se desea controlar. Un último aspecto interesante, especialmente para un centro de producción con un parque de máquinas existente, es que la unidad inteligente está disponible en dos configuraciones: unidad base o unidad remota. La unidad base se conecta al ordenador de supervisión mediante un cable Ethernet, pero la misma unidad base puede recoger señales de hasta otras diez unidades base mediante una conexión inalámbrica, con un alcance de hasta cien metros. Los datos de once máquinas pueden recopilarse desde un único punto de conexión físico, con considerables ventajas en términos de facilidad de instalación y costes de disposición de la red. Los sistemas base y remoto están disponibles actualmente en las siguientes configuraciones: Ethernet-IP, Profinet y EtherCAT, junto con el protocolo en OPC UA Por último, el sistema es totalmente abierto e interactúa con cualquier software de gestión de energía existente en el mercado. De este modo, la actualización tecnológica y personalizada de las máquinas ya existentes resulta fácil y rentable.
Recapitulando y retomando la pregunta original, adaptar una máquina para que satisfaga óptimamente las necesidades implica el mejor diseño posible y equiparla con sistemas modernos que permitan monitorizarla, detectar posibles anomalías con antelación y que consuma la menor cantidad de energía posible. Con el sistema AMS, alcanzar estos objetivos está verdaderamente al alcance de todos.
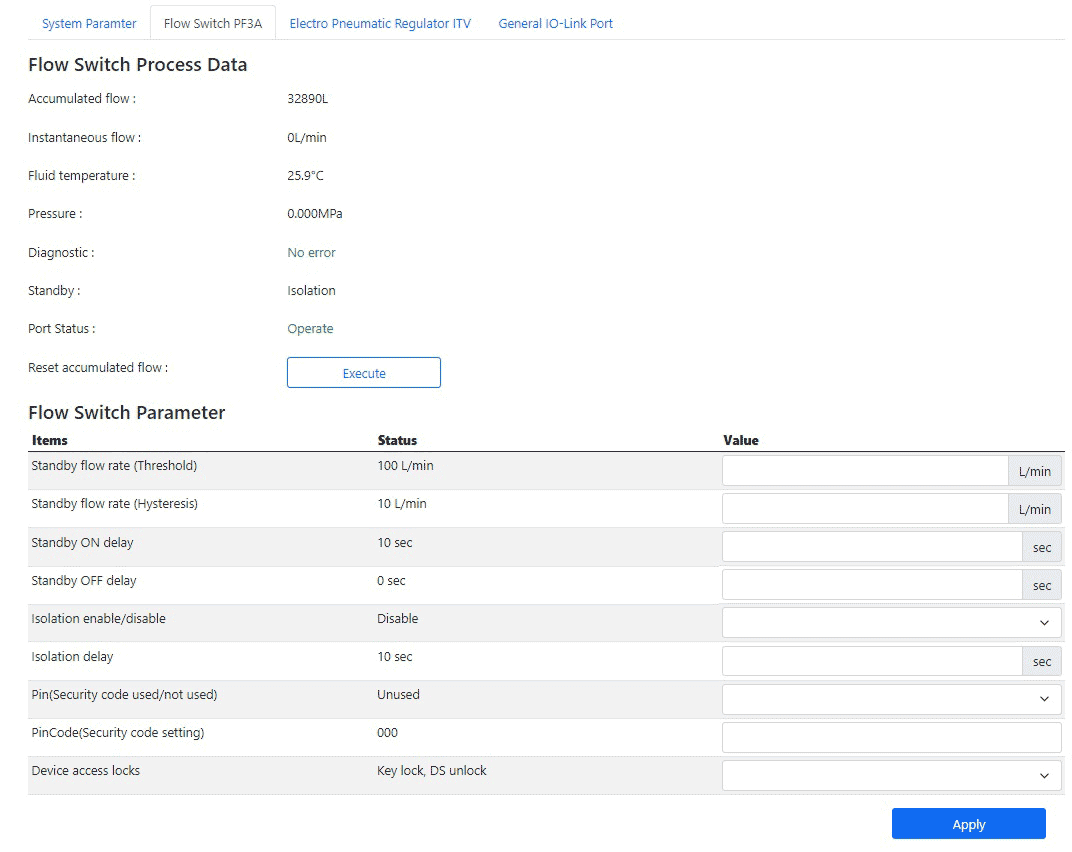
Foto 3 - Página de programación a través de la función Servidor Web. Se trata de parámetros simples de funcionamiento que deben introducirse únicamente en los campos predefinidos.