Girbau optimises the energy efficiency of its automated ironing line in collaboration with SMC
Sustainability and reduction of energy consumption have been key values for Girbau for many years. The company has recently launched a new ironing unit that is part of a complete automated line. Close collaboration between Girbau and SMC has made it possible to improve ironing quality and achieve an energy saving of 30%, a reduction of 25% in compressed air consumption and a 25% increase in the useful life of textile coatings.
Girbau, whose headquarters are in Vic (Barcelona), is the world's fifth-largest manufacturer of industrial laundry solutions: washing, ironing and drying systems. The company operates in more than 100 countries and has 15 subsidiaries in Europe, the Americas, Oceania and Asia. Throughout its 60 years of history, it has maintained the values of a family company since its beginnings, placing people and closeness to its customers at the core of its activities. Its firm commitment to innovation, energy efficiency and sustainability make Girbau a leading company in its sector.
As part of its product range, Girbau develops and manufactures ironing lines. These lines are made up of 4 units: a front feeder that leads to the ironing unit, which we will talk about below, followed by the folder and stacker. These lines, which may measure as much as 15 metres long and 4 metres wide, iron and fold up to 1,200 articles per hour.
Optimisation of the ironing line was carried out in two countries: the ironing unit was optimised by Girbau Spain and optimisation of the other 3 units was performed in France. In both cases, Girbau could rely on the unconditional support of SMC.
Optimisation of the ironing unit
"Our modular ironing machines for drying and ironing (heaters) handle fabrics of many different kinds, from napkins to tablecloths and duvet covers". "The wide variety of these fabrics made it necessary to redesign the heater to ensure the best result with any type of item. We wanted this improvement in quality to go hand-in-hand with an increase in energy efficiency, which always guides our designs", according to Quim Riera, the product manager for ironing equipment at Girbau.
The ironing unit is based on a rigid steel bed, which is heated internally, on which a perforated roller with a textile coating turns. The turning of the roller slides the item being ironed over the interior face of the bed. Drying and ironing of the item takes place due to evaporation of the water in the item because of the temperature of the bed and the pressure that the roller exerts on it. "Process optimisation was based on introducing 6 pressure levels in the ironing rollers. Application of the correct pressure on each fabric guarantees customers that the various items will suffer less, thus increasing the quality of their finish. In energy terms, it translates into a reduction in consumption of up to 30%," Quim Riera added.
Customised solutions and complete "plug and play" modules
Large pneumatic actuators were installed in each heater, capable of handling heavy loads up to as much as 2,400 kg and ensuring correct movement of the item through the different modules as the residual humidity is eliminated until it is perfectly ironed.
"The heater produces a lot of heat and humidity during the process; so we have designed special cylinders that withstand temperatures of up to 90°C and ensure the resistance the ironing machine requires", commented Albert Albó, SMC's technical advisor for Girbau in Spain. "At SMC we are able to design, produce and assemble the cylinders in Europe; that is a great advantage, since we can supply Girbau with a tailored solution with a short delivery time. That is part of our ongoing commitment to being close to and supporting customers," Albert concluded.
The installation of proportional valves in the ITV series guarantees control of the force exerted. The proportional valves are part of a customised electro-pneumatic module that was developed and assembled by SIMA (an SMC distributor and integrator). Together with the ITVs, 5-way solenoid valves, a digital pressure switch and a 3-way solenoid valve are assembled in accordance with ISO13849-1. The basic function of this set is to automatically control the pressure that the roller exerts on the item, depending on the type and thickness of the item to be ironed; the proportional valve regulates the pressure, depending on whether greater or lesser resistance is exerted when the item passes through. It also includes a safety system so that roller maintenance stoppages can be performed safely.
Improvement in the ironing machine's energy efficiency
"The most important thing for Girbau is customer satisfaction and this new solution has been extremely well received by the market", said Quim. "The results obtained have been palpable to our customers right from the start. The most visible aspect is the better treatment of the textile and the increase in ironing processing cycles. However, optimising the pressure produced another set of benefits such as cost reduction arising from electricity savings of up to 30% and a reduction of up to 25% in air consumption."
Finally, Quim argues that "we have made an improvement to maintenance tasks for our customers due to decreased wear of parts; for example, we have increased the usage time of textile coatings in the heater by 25%".
Ongoing improvement of the complete line
Developing a line with 4 units involves a large number of automation tasks and it is essential to simplify the development and installation processes. These improvements were mainly carried out in France.
As Patrice Subra, director of operations at Girbau Robotics in France, explains, "SMC is differentiated by its high-quality service, its fast reaction speed at all times and the high reliability of its solutions. They have supported us from the initial stages of our developments. When we define an electro-pneumatic module, SMC analyses the components that have the best size and simulates energy consumption. Through this 'fit for purpose' focus, SMC improves overall energy efficiency and reduces the cost to the end customer. We have also managed to reduce returns of defective products."
SMC thus designed 20 different modules to cover all line needs. These control panels, designed to Girbau's specifications, simply need to be configured and then they are ready to be connected to the ironing unit. Delivery of customised models that are ready to connect greatly simplifies their installation, reduces assembly costs (by minimising the risk of failure during assembly, since SMC tests all of the modules before delivery) and aids purchasing processes since each module has a unique reference number. "Stock management is enormously simplified. In addition, SMC is able to supply the modules by the required deadlines," Patrice Subra added.
Later, when the first prototypes are already in operation, SMC analyses consumption and helps optimise some pneumatic functions, if necessary.
SMC also collaborated on improving existing lines to reduce energy consumption. "Sensors were fitted that detected the lines with the greatest consumption, resulting in an improvement in the folding process. The system that used air blades to fold sheets was replaced with a mechanised system", Patrice Subra added.
"With its wide range of reliable solutions and service focus, SMC will undoubtedly be our partner in tackling future development challenges," Patrice Subra concluded.
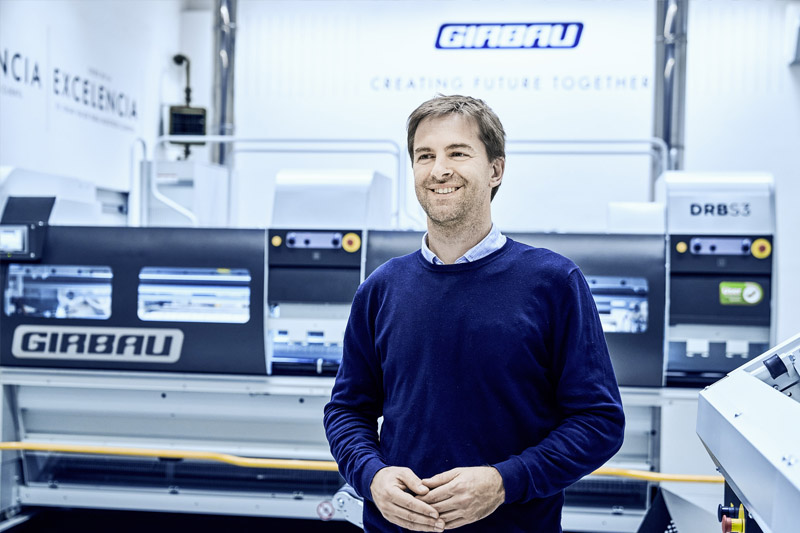
Quim Riera, the product manager for ironing equipment at Girbau
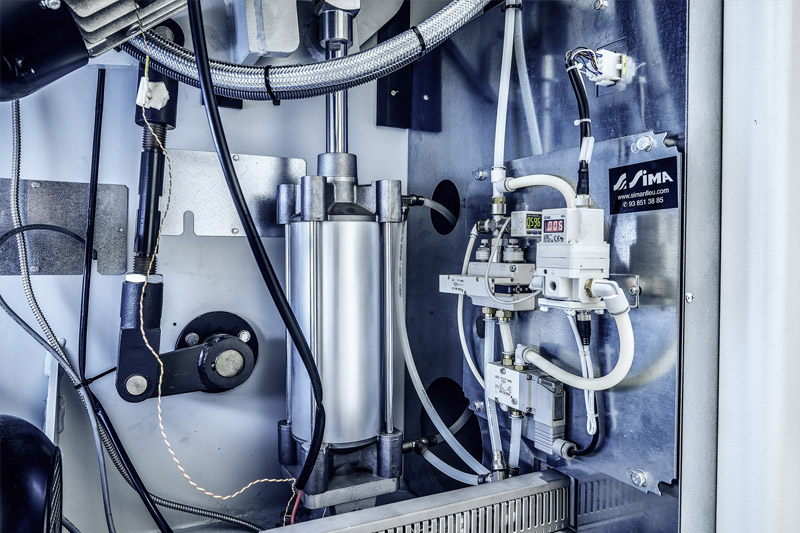
Customised solutions and complete "plug and play" module
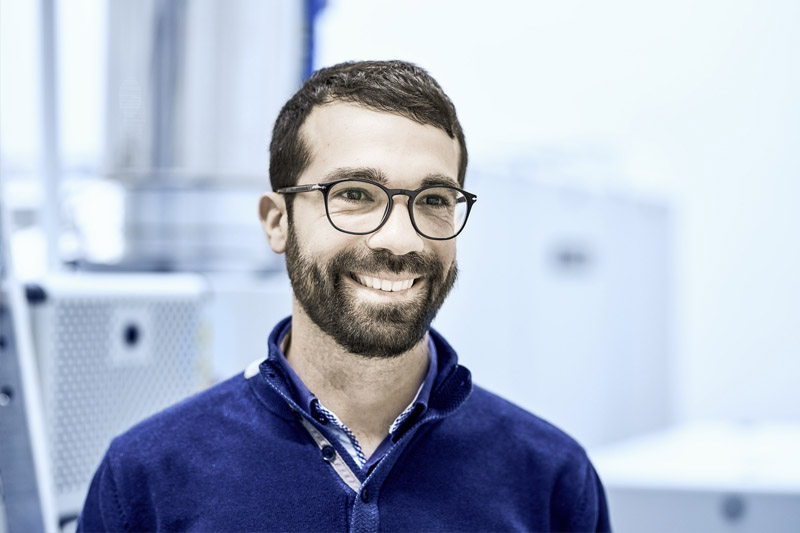
Albert Albó, SMC's Spain technical advisor for Girbau
3 may. 2021