Who has not heard about the PCR test? In vitro diagnostics (IVD) in general and analyser in a more specific sense, have always played a key role in society as they are non-invasive tests performed on biological samples (for example blood, urine or tissues) to diagnose or exclude diseases. Covid-19 has put IVD in the spotlight and diagnostic tests are, unfortunately a normal part of our daily conversations. The professionals in IVD already knew that an early diagnosis can make the difference; that the right diagnosis can make the difference. Now we all know. In this context it is no wonder that a key target for IVD in general, and analysers in particular is for them to provide fast results as well as accurate ones. Appropriate fluid handling of these techniques plays a fundamental part in achieving the desired speed and accuracy. As fluid handling involves many critical components interrelating together, it is vital to involve a skilled partner able to supply proven solutions for the entire system, at early stages of development. And that´s SMC.
By Philippe Pinto – Industry Manager Life Science, Europe
JULY 2021
In the land field of analysers
Let’s define what is an analyser. This is an instrument or device that conducts chemical analysis on samples or sample streams to provide haematology values (e.g. red blood cell count, haemoglobin concentrations) or to determine the concentration of analytes (e.g. cholesterol, glucose). This capability assists in the diagnosis and treatment of diseases that include e.g. diabetes, infectious diseases, oncology, diabetes, anaemia, autoimmune deficiencies, cancer and hepatitis, drug testing HIV/AIDS, and of course Covid-19.
There are three common types of analyser:
- for clinical laboratory testing
- for near-patient testing and
- for self-testing.
Optimising fluid handling as the key part to ensure the desired speed, repeatability and accuracy
Whatever the testing technologies – e.g. clinical chemistry, haematology, immunoassay urinalysis, DNA, biology, molecular – the fluid (liquids or gases) handling system have a critical importance as it contributes to ensure desired speed, repeatability, and accuracy of an analyser. These complex systems handle the sample extraction, the mixing with reagents, the introduction into the analyser and finally washing of its own circuit. In this context, it is crucial to select a supplier with a complete and proven range of solutions.
The challenge of addressing speed and repeatability
One of fluid handling’s main technical challenges is the interaction among the given functions. This fact creates a situation where an increase in the speed could endanger repeatability. The combination of speed and pressure may affect the test precision as the speed increases the risk bubble generation or turbulence which affects the repeatability. The selection of the optimised designed components with for example, minimisation of dead volume, or circuit topology optimisation, minimises these problems without leaving a side to choose the right compatibility material in contact with the fluid.
Ensure no sample contamination with the appropriate fluid control to help enhance analyser speed and reliability
On an analyser, the isolation valve controls the on/off function and flow path direction for different functions, from fluid sampling circuit to waster line circuit. This valve manages the flow of bleach or saline wash solution that cleans the test equipment’s tubing, as well as the end probes of pipettes and pumps before a new sample can be analysed. So, minimising the dead volume to ensure no contamination is vital.
Isolation valves’ most important feature is the diaphragm in EPDM, FKM or FFKM, the rest if the wetted part is in peek which completely isolates its internal parts from the analyser’s flow path to mitigate the risk of contaminating the process fluid. Notably, the space between the valve’s internal chamber and flow path is purposely constructed to minimise dead volume, where trapped chemicals could carry over to the next test’s fluid flow when the valve is closed and re-energised.
The internal flow path of an isolation valve from SMC is notable for its smooth surfaces, preventing the generation of bubbles and other flow concerns. SMC offers proven, high-quality solutions with a large internal volume, all backed by specialist sales teams. A large range is available covering many options and sizes. Central among the features of SMC isolation valves is low power consumption to avoid any heat transfer to the fluid.
Ensuring repeatability, no contamination and efficient fluid mixing and dosing through customised acrylic manifold
An acrylic manifold is a multi-layered bonded manifold, and is equivalent to a printed circuit board, but for fluids. It ensures that the sample and reagent are introduced in the analyser in the right proportion. This solution should be preferred to the tube-to-tube connections for performing analysers as it offers many advantages. For example, an acrylic manifold greatly reduces the number of joints, thus combatting common analyser issues such as leaks and tampering with tubes, which results in better repeatability.
These solutions also reduce the overall size of the fluidic assembly, saving space in a very crowded analyser, while a further benefit is the provision of easy visual inspection to check for flow path contamination, for instance.
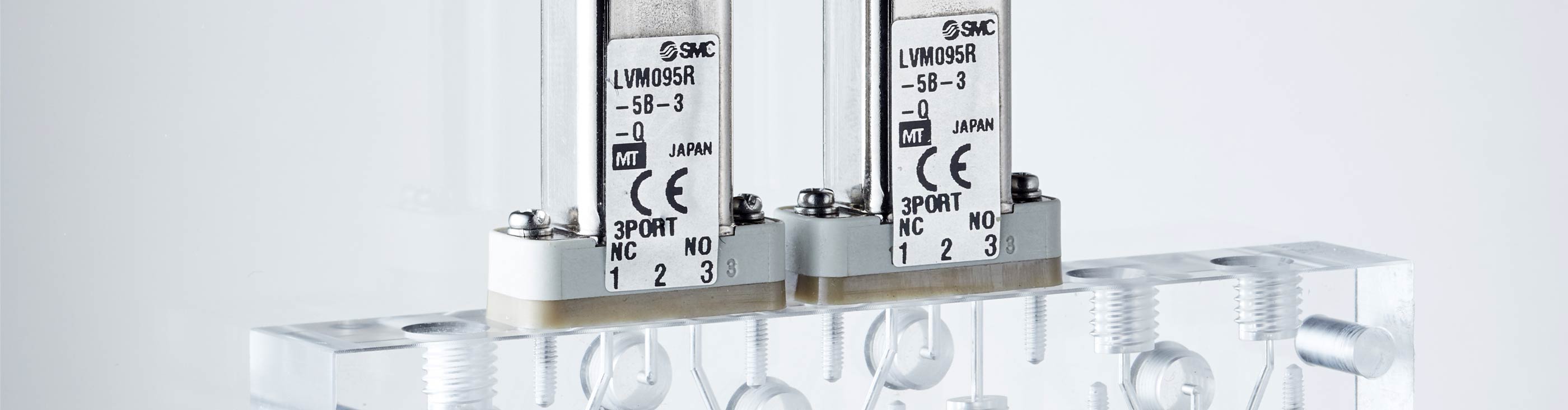
The customisation of this component is essential. Each acrylic manifold we provide is custom designed as it needs to meet the specific application needs in terms of circuit, mounting components, space constraints, optical clarity, chemical compatibility and flow speed path. In relation to the flow speed path, our optimised curved design allows smoother liquid flow. In the fine-tuning part of our process, we ensure minimisation of dead volume by addressing the risk of bubble generation.
Manifold layers are assembled via heat and pressure, as it is preferable to avoid chemical reactions. Common materials include acrylic, but also PVC, polysulfone and Ultem™.
We build a proof of concept (POC) with full functional testing, delivering a tested manifold. The customised design includes the possibility to embed all necessary components, as it can be pressure and flow sensors or valves, so we hand over a ready to plug and play solution.
Ensuring high accuracy through micro-dispensing
Precision liquid dispensing ensures that the flow and measurement of liquid/gas samples, reagents and wash solutions. A solenoid diaphragm pump supplies a single measured shot of liquid each time the solenoid is energised, therefore is perfect for dosing or for mixing solutions.
Our solenoid liquid dispensing pumps offer adjustable pump volume from 5 µl to 200 µl per stroke, the self-priming miniature pumps are designed for very high precision - with a repeatability of ±1 %. Their maintenance-free design ensures easy and long-lasting use, while their compact housing saves space and simplifies integration into complex systems. Depending on requirements, they can be configured with different chemically resistant materials (wetted part are peek or pp and for the diaphragm and seals can be in EPDM or FKM) to realise the optimal combination of functions and properties for the specific application.
Automate operation with pneumatic or electric control
In terms of automating operations such as sample management and loading, opening the reagent chamber doors, washing the circuits, and ejecting used cuvettes into the waste stream the analyser builder can turn to air-based or electric based solutions.
However, an increasing industry trend for analysers is to not integrate a compressed air source due to noise, vibration, dimension, maintenance or leaks issues. Whichever is the chosen technology to automate, we support analyser builders with a full range of pneumatic solutions as well as electric actuators and controls. Electric automation can include for example, electric rotary tables that provide continuous 360º rotations, making them ideal for indexing wheels on sample and reaction trays. We also provide compact and lightweight electric grippers with adjustable gripping force, suitable for handling a variety of vials and tubes.
However, what makes all the difference in order to match their fluid handling system perfectly, is our expertise in developing, or better said, co-developing customised designs. Local engineers backed up with our global network of technical centres to find the best technical ad-hoc solutions for each handling system casuistic.
If the preferred solution is air-based, one key component will be to include a membrane air dryer to ensure moisture removal. This function is vital because even a small amount of compressed air moisture can be problematic for an analyser; humidity can reduce the lifetime of the components and functionality of the products, with a likelihood of impacting the analyser´s reliability. Furthermore, as most analysers usually operate at low pressure and low flow, it is important to consider whether a low-purge option is needed.
Ensuring reagents temperature control to extend their shelf life
Temperature control of the reagent might also be an issue, especially for large-scale analysers that do hundreds of tests per hour, carrying various reagents. The typical shelf life of an unrefrigerated reagent can be just two days. However, if the reagent is kept chilled, shelf life can be extended to 35 days. Many analysers are equipped with integrated chillers or thermal control units in their reagent chambers to preserve the shelf life of reagents. For all these needs, SMC counts with adapted solutions.
Building the correct mix of components within the fluid handling part of an analyser, will greatly ensure the speed, repeatability and overall accuracy in the test diagnostics. Furthermore, addressing these issues results in improving the cost effectiveness individual test value and in lowering maintenance and the safest operations day after day. A key part for lays in the engagements at early stages for co-developing and achieving an optimum outcome. At SMC we have been fully involved in close cooperation with analyser device manufacturers in their project development for many decades. Our Life Science experts are on hand and ready to support this vital industry and give our small contribution to good health and well-being.