Between 2020 and 2027, the food processing market is expected to grow with a compound annual growth rate (CAGR) of 6.04% according to Verified Market Search. The industry will have to increase its productivity while simultaneously dealing with a lack of workers and cost pressure.
By Diego Mirabelli – Industry Manager Food, Europe
MAY 2021
As most automation companies are focused on machine builders, SMC is differentiating itself by being present with the food manufacturers on their factory floor in order to identify the food industry’s most pressing challenges and help to overcome them. In order to improve their productivity, factories must reduce downtime, implement more automation and improve energy efficiency, machine safety and hygiene.
What impact has the COVID-19 outbreak had on factories and their ways of working? Surprisingly, COVID-19 has accelerated the move towards more automation because workers (already difficult to hire), are increasingly absent and the need for social distancing makes automation even more crucial.
Avoid downtime
A stop in production is any food factory’s worst nightmare, as most factories operate on a 24/7 basis with production areas arranged in a continuous flow with one area being dependent on the activity of another, from primary material integration, to processing, and finally, packaging.
Any component failure will generate a stop in production costing the factory time and money. The OEE (Overall Equipment Effectiveness) can be substantially improved by applying digital predictive maintenance solutions, training operators, and maximizing product reliability.
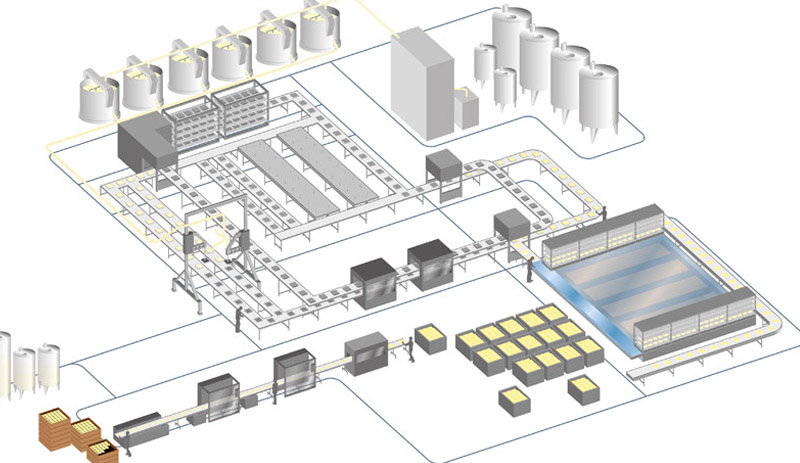
Caption: Food plants are predominantly working with a continuous flow making on a 24/7 basis. Thus, any downtime of an individual component is very expensive
The most critical component in any factory is the actuator. The procedure to replace an actuator is very fast (usually 10 minutes) when its within easy reach. In other cases, it can take up to 4 hours. Of course, the cost of replacing an actuator will usually be a lot less than the cost of a stop in production.
Most food factories perform maintenance on a regular scheduled basis, which means some components are replaced even if they are still good to run. To ensure real-time condition monitoring, users need clear visibility of equipment status at all times. This can usually be achieved with 2 types of sensors developed by SMC. Firstly, induction sensors which calculate the speed of the rod, enabling easy detection of dirt on the guides, and secondly, pressure sensors that will identify any leakages inside the actuators. These sensors communicate via IO-Link. Data is available in real-time in order to check the condition of the equipment.
Furthermore, SMC has developed a partnership with Dell and Software AG, a global factory monitoring tool. The key differentiating factor of this Industry 4.0 solution is that it displays the data in a very user-friendly way, and it triggers alerts when equipment is at risk of failure. This solution is based on SMC know-how and uses artificial intelligence features, one of which is machine learning. Operational data is quickly available for analysis: behavior of the actuator is analyzed in parallel with other operating data, in order to accurately predict a failure after a data collection period of just a few months.
There are many advantages of having trained operators on the factory floor who are able to handle simple maintenance tasks by themselves. SMC shares its expertise with practical training courses containing theory, exercises, and practical activities. The training is aimed at line operators (even those with no experience in pneumatic components), who can identify potential issues before machine failure occurs, and handle simple maintenance. Therefore, having trained operators helps to improve machine reliability.
Finally, addressing downtime requires good component reliability. SMC products improve reliability by making use of technical innovations such as a lower-than-competition “minimum working pressure” or metal seal technology instead of rubber on actuators and valves. However, product reliability cannot often be measured in such absolute terms as it depends on the customer’s specific application regarding frequency, temperature, humidity, etc. Therefore, maximizing reliability is the responsibility of our engineers, who will be able to specify the right product for the application, both with the machine builder and the final users.
Productivity increases through increased automation
This fast-paced industry has traditionally been lagged in automation penetration, which we normally see in the primary and secondary processing stages.
Robotics, and its stemmed technology, Cobots, can make a great impact in the coming years in assisting our food customers to achieve longed for productivity levels.
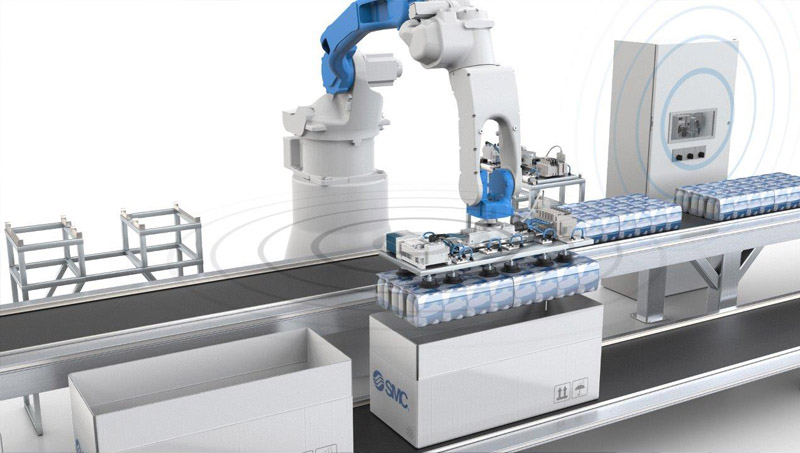
Caption: Robots can automate many tasks
So, what makes SMC a suitable specialist in this area? Well, having a team dedicated to the development of robotic solutions, and notable partnerships is a main strength. We have expertise with all different gripping technologies (pneumatic, electric and magnetic) and we have also developed a wide range of plug and play gripper end-effector for different Cobot suppliers like Universal Robots.
Our wireless technology is a key player in robotics applications allowing gripper communication by Wi-Fi and fast installation due to the absence of wires.
Other tasks in a food factory can be carried out by additional standard automatic machines, such as stack feeding, product orientation, feeder, pick and place. This means a close relationship between automation providers and machine builders is essential in order to automate what is usually done manually. However, machine versatility is also a key issue to consider. Take Dispensing for example, imagine a scenario where you have different dispensing needs on the same production line, flexibility is needed to create a different shape on one chocolate biscuit to another. It’s not unusual for the same product to have different features in different countries. Automated machines may often be assisted by Cobots and Vision systems to optimize the process and increase flexibility.
The next step is to introduce smart technologies in automation. The increase in individualized products requires flexible, effective and intelligent manufacturing for a quick reaction to market changes. Machines must combine flexible and quick format changes with high cycle rates and low life cycle costs. Digitalization and the Industry 4.0 revolution will ease the switch from one production to another and improve the global factory operation flow, and Smart automation will bring more flexibility in machine adjustments.
SMC is already offering devices connected to IO-Link and fieldbus to get all relevant data from the factory floor. SMC IO-Link sensors, IO-Link master and IO-Link actuators are just some of SMC’s smart products that can help. The focus of the SMC expert team is to evolve the Industry 4.0 path.
Reducing costs by optimizing energy efficiency
Food factories are energy demanding; they represent 19% of the whole manufacturing industry’s energy consumption. Improving energy efficiency will not only reduce costs, but it will subsequently reduce the carbon footprint, which is a key objective for food plants, for which pneumatics represents 20% of the global power consumption. That being said, improving energy efficiency means identifying where and how energy is consumed. To do this, SMC carries out production line audits on the factory floor and produces a detailed report with measurements, data and pictures and sets out all remedial actions to aid optimization, including how much money could be saved, and how much investment is required to achieve each added-value objective. Improvement costs may vary but the return on investment is often short. An example of a suggested improvement could be simple product optimization like LED indicators showing that equipment is constrained and consuming too much energy because of a problem. The most common issue is usually air leaks, which lead to excessive energy consumption, for which SMC provides a wide array of solutions: condition monitoring tools which provide information such as flow rate and pressure, Automatic Leak Detection System (ALDS) which provides near real time leakage monitoring and a VEX Stand-by Valve, which reduces air consumption during short stops or shuts it off during long ones.
It should be noted that we have accumulated a huge amount of data, expertise, and know-how in this subject, as this type of audit has been carried out with many of our customers worldwide, and we have created an internal knowledge management system (Improvement Activity Reports). Thanks to this expertise and knowledge management system we can approach the machine builder with added value optimization. It could be a simple suggestion, such as the sizing of the pneumatic component, or the production line co-engineering proposing energy efficient automation tasks or advising on the best technology to apply between electric drives or pneumatics.
Energy efficiency will also come from the products themselves. SMC has made a big commitment to develop light and compact products which impact the saving of utilized compressed air, especially for moving parts like grippers and actuators. The power-saving circuit can also reduce CO2 emissions.
Machine safety and hygiene also require SMC engineering expertise
A reputable automation specialist should always adopt a realistic approach by helping End Users to support the implementation of the Safety function with the machine builders. Appropriately designed products and validated operational valves (according to ISO 13849) are central to delivering overall safety, particularly regarding machine control. It is always required to use validated operational components (VOCs) and product data (SMC counts with its free library “SISTEMA”) when building safety control systems.
For higher Performance Levels of safety SMC provides redundant valves, which give the possibility to exhaust the air in case of a machine stop.
Although hygiene has always been a central theme of the food industry, COVID-19 has pushed the message home. Both machine builders and food plants need solutions that are easy to clean and reduce opportunities for contamination. While bespoke designs and materials often come at a higher price than standard solutions, the price of failing to ensure hygiene can be far higher. To help machine builders on a practical level, a supplier that can offer hygienic-qualified products – such as air preparation equipment, actuators, solenoid valves and fittings – should be selected. Key factors to look out for include components in stainless steel to avoid corrosion; greases (resistant to water and chemical agents) that comply with FDA standards; laser marked, not labelled components, and treated air quality according to ISO standards. Another factor to consider is that navigating and understanding relevant hygiene standards can be notoriously challenging as there are many different types of food plant. In addition, food plants now have to meet the different hygiene requirements and regulations in different countries relating to COVID-19. To help stay abreast of standards worldwide, SMC uses its membership of organizations such as EHEDG (European Hygienic Engineering and Design Group) to support customers in understanding the relevant standards and how they should be implemented moving forward.
Another issue is that standard product adaptation is often necessary. SMC offers this service and is be able to support the customer in understanding which standard it needs to meet and how to implement it.
In conclusion, products and automation expertise are not enough to meet the food industry’s many challenges. Familiarity and close working practices with our End-customers is the only way to ensure the best availability of the production line and achieve cost and energy reduction and compliance with the strict regulations of the food industry. That is the SMC commitment.