In den vergangenen Jahrzehnten hat sich Predictive Maintenance zu einem gern genutzten Schlagwort entwickelt. In Produktionsanlagen ist man ständig bestrebt, Gesamtbetriebskosten zu minimieren, indem man Störungen und Ausfällen aktiv entgegenwirkt, quasi „just in time“. Viele gehen jedoch fälschlicherweise davon aus, dass die Einführung einer vorausschauenden Wartungsstrategie eine komplette Umstrukturierung ihrer Arbeitsprozesse erfordert. In Wahrheit können aber wenige kleine Maßnahmen schon einen Riesenunterschied ausmachen: Wenn es um Maschinenlaufzeiten und die Gesamtanlageneffektivität (GAE) geht. Um die nötigen Schritte erfolgreich umsetzen zu können, empfiehlt es sich, mit einem vertrauenswürdigen Technologiepartner zusammenzuarbeiten. Für SMC als Weltmarktführer im Bereich der pneumatischen Automatisierungstechnik steht das „P“ in „Predictive Maintenance“ für ‚progress‘ und nicht für ’pain‘.
Von Oliver Prang, Expert Digital Business Development, SMC Deutschland
Laut einem Bericht in der IndustryWeek kosten unvorhergesehene Ausfallzeiten Hersteller jährlich geschätzte 50 Mrd. US-Dollar. Anlagenausfälle sind der Grund für 42 Prozent dieser verlorenen Produktionszeit. Die Notwendigkeit eines effektiven Wartungsprogramms kann daher kaum bestritten werden.
Unterschiedliche Strategien
Es gibt verschiedene Arten der Wartung: Die reaktive, die präventive und die vorausschauende Wartung sind wohl die am häufigsten verbreiteten. Doch wie hängen diese anscheinend ganz unterschiedlichen Begriffe zusammen? Manche Experten nutzen zur Veranschaulichung den Vergleich zwischen der Gesundheit des Menschen und der von Maschinen. Diabetes ist beispielsweise eine Erkrankung, die laut Weltgesundheitsorganisation derzeit weltweit rund 422 Mio. Menschen betrifft.
Eine Entsprechung für die reaktive Wartung wäre in diesem Fall die Behandlung nach bestätigter Diagnose. Der Patient wird sich in der Folge Spritzen setzen oder Tabletten einnehmen müssen, um seinen Blutzuckerspiegel zu kontrollieren. Auch ist eine kontrollierte Ernährung erforderlich, bei der die Menge des aufgenommenen Zuckers oder der Kohlenhydrate reduziert oder auf diese sogar ganz verzichtet wird. Dagegen bestünde eine präventive Wartung darin, der Erkrankung entgegenzuwirken, wenn noch gar keine Symptome aufgetreten sind. Hält sich der Patient dann an einen gesunden Lebensstil, unterstützt von einer kontrollierten Ernährung und einem gezielten Sportprogramm, kann er die Entstehung der Erkrankung hoffentlich verhindern. Die vorausschauende Wartung setzt ein, wenn sich der Patient in einem „prädiabetischen“ Zustand befindet, aber noch innerhalb eines sicheren Bereichs oder vertretbarer Kriterien liegt. Durch eine regelmäßige Überwachung des Blutzuckerspiegels und des Body Mass Index lässt sich beispielsweise erkennen, ob sein Zustand stabil ist oder sich mit der Zeit verschlechtert. So kann bestimmt werden, ob und wann weitere Eingriffe in die Lebensweise erforderlich sind.
Das Ziel von Fertigungstechnikern ist es, die Zuverlässigkeit einer Maschine zu erhöhen, indem das Risiko kostspieliger Ausfallzeiten, die zu Produktionsunterbrechungen führen, minimiert wird. In vielen Fällen gelingt dies durch die Kombination verschiedener Wartungsstrategien in unterschiedlichen Produktionsszenarien, statt durch die Wahl einer einzigen Strategie, die gerade in den sozialen Medien im Trend liegt. Hier gilt es viele Faktoren zu betrachten, nicht zuletzt auch die Umsetzungs- und Managementkosten im Verhältnis zur Anzahl der Ausfallereignisse.
Nichts geht ohne Daten
Der Schlüsselbegriff lautet hier gar nicht einmal vorausschauende oder präventive Wartung, sondern „Daten“. Die Einführung von Predictive Maintenance erfordert drei grundlegende Dinge: Daten, Zeit und Analyse. Daten sind Ihr wichtigster Verbündeter, um Ereignisse vorherzusehen – quasi die moderne Version einer Kristallkugel – und so die Zuverlässigkeit von Maschinen zu erhöhen. Es ist jedoch umfassendes Wissen nötig, um zu erkennen, wann und warum eine Anlage an Zuverlässigkeit einbüßt. Aus genau diesem Grund kann sich die Zusammenarbeit mit einem zuverlässigen Automatisierungsspezialisten spürbar auszahlen.
Aus praktischer Perspektive lautet die erste Regel, die Dinge möglichst einfach zu halten. SMC unterstützt seine Kunden mit einem schrittweisen Ansatz, beispielsweise von der Antriebsleckageanalyse über die partielle Maschinenanalyse bis zur umfassenden Analyse ihrer Anlagen. Auf diese Weise werden alle erforderlichen Kenntnisse, alle Prozessdefinitionen und persönlichen Verantwortlichkeiten von einem ersten kleinen Projekt nach und nach auf möglichst reibungslose Weise in ein größeres Projekt überführt.
Ein gutes Beispiel dafür ist der Pneumatikzylinder: das „Zugpferd“ vieler industrieller Anlagen. Zu den häufigsten Störungen bei Zylindern gehören Lecks an der Kolbendichtung. Diese Defekte können schwer zu erkennen sein und zu einem Druckverlust führen. Ein Betriebsdruckverlust von nur 0,1 MPa kann die theoretische Kraftabgabe eines Zylinders (32 mm Kolbendurchmesser) um 17 % mindern. Eine weitere Nebenwirkung einer fehlerhaften Dichtung ist ein Anstieg des Druckluftverbrauchs, um die Leckage zu kompensieren.
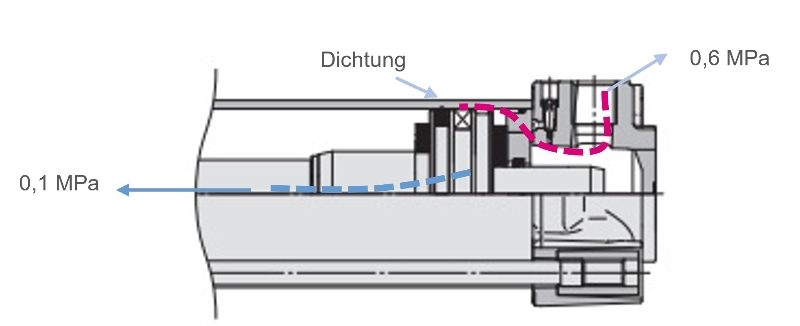
Nennkraft in Newton
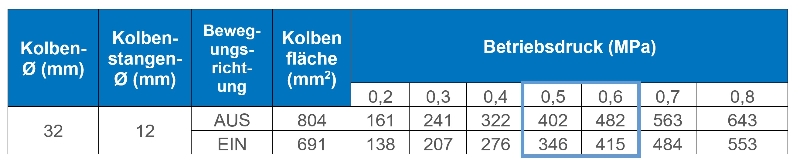
Auszug aus dem CP96-Katalog von SMC
Eine präventive Wartungsstrategie erfordert hier wenig mehr als die Installation eines Drucksensors an jedem Zylinderkanal und die Überwachung der Druckentwicklung über den Zeitverlauf. Defekte an der Dichtung werden aufgrund einer abnormen Leistungskurve im Vergleich zu den „angelernten“ Kurven für den Normalbetrieb schnell auffallen. Mithilfe einer Machine-Learning-Analyse in Echtzeit ist es möglich, rechtzeitig vorausschauende Wartungsmaßnahmen vorzunehmen, noch bevor es zu größeren Leistungsverlusten oder Maschinenausfällen kommt.
Neben Drucksensoren können beispielsweise auch induktive Sensoren zur Berechnung der Zylindergeschwindigkeit und zur Erkennung von Verunreinigungen gute Dienste leisten. Eine weitere Empfehlung besteht darin, ein Netzwerk von Durchflusssensoren zu installieren, die die Verwendung der Druckluft (und alle Lecks oder Fehlfunktionen) über den Pneumatikkreislauf kontinuierlich überwachen.
Wirkliche Intelligenz
Natürlich ist nicht jede Intelligenz künstlicher Natur. Sicher können Maschinen lernen, prognostizieren und präventiv eingreifen, doch dabei sind sie trotz allem immer noch auf den Input von Menschen angewiesen, um Überwachungsvariablen zu definieren und Grenzwerte festzulegen. Außerdem muss der Mensch darüber entscheiden, welche Maschinenkomponenten mit Sensoren ausgestattet werden sollen, da nicht alle entscheidend für Maschinenlaufzeiten und Produktivität sind. Auch Budgets, Zeit und Personalverfügbarkeit spielen eine Rolle.
Vor diesem Hintergrund erweist sich die Zusammenarbeit mit einem zuverlässigen Technologiespezialisten als vernünftige Strategie. Kombiniert man beispielsweise die Fachkenntnis von SMC in Sachen Automatisierungskomponenten mit dem individuellen Know-how eines Kunden im Hinblick auf die verwendeten Maschinen, ergeben sich dadurch beste Voraussetzungen für den Erfolg.
Ein weiterer potenzieller Faktor ist hier die verlässliche Instandhaltung. Eine von Grund auf optimierte Konzeption ermöglicht die Reduzierung unnötiger Wartungskosten auf der Grundlage der FMEA (Failure Mode Effects Analysis). Im Wesentlichen konzentriert sich dieser Ansatz auf die verschiedenen Fehler, die auftreten könnten, sowie deren potenzielle Folgen. SMC erleichtert Ihnen diese Aufgabe durch Konfigurationstools für Pneumatikleitungen, Ventil-Mehrfachanschlussplatten und Zylinder, die Ihnen auf der Website zur Verfügung stehen und Ihnen helfen, die Auswahl – und Leistung – der entsprechenden Produkte für eine bestimmte Anwendung zu optimieren.
Viele gehen davon aus, dass Predictive Maintenance die ultimative Lösung zur Reduzierung von Ausfallzeiten und zur Verbesserung der Gesamtanlageneffektivität ist. Derzeit ist das aber noch nicht der Fall, auch wenn sich die Situation aufgrund einer zunehmenden Anzahl von intelligenten Smart-Factory-Initiativen in Fabriken in aller Welt in den kommenden Jahren durchaus in diese Richtung entwickeln könnte. Bis es so weit ist, liegt der Schlüssel zum Erfolg immer noch darin, das vorhandene Know-how zu bündeln. SMC steht Ihnen dafür als Partner zur Verfügung.