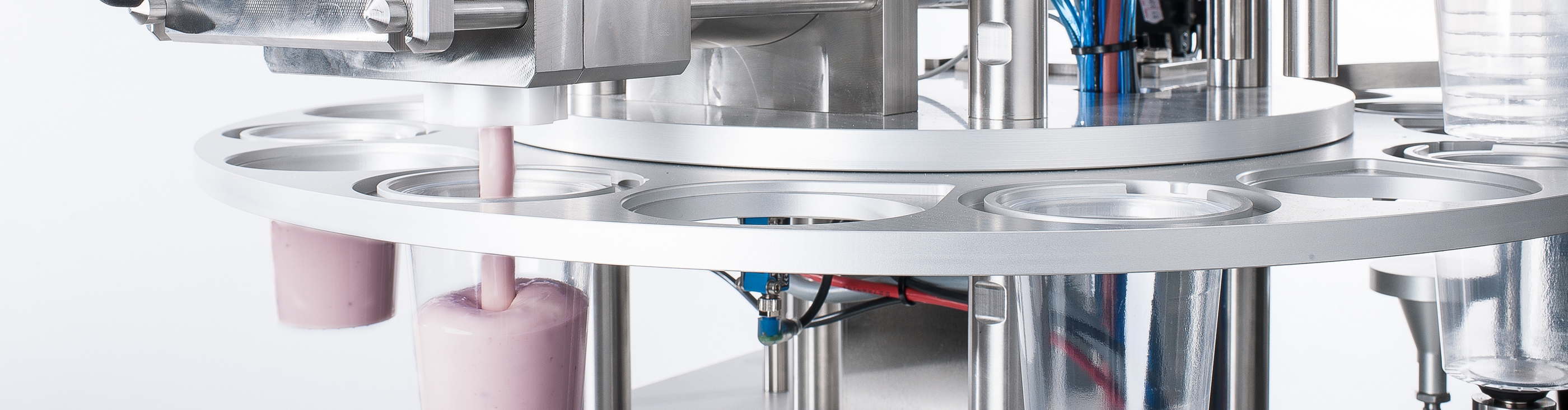
In the vast market for packaging machinery, the Swiss company EmbaPlan GmbH specialises in the development and manufacture of flexible filling machines for small quantity production runs, adapted to the needs of innovative and regional producers of high-quality foods. The company recently made a major upgrade to one of their filling machine models, adding a valve manifold from SMC for extra flexibility and performance.
EmbaPlan GmbH in Walkringen/Switzerland has carved out an attractive niche for itself in the vast market for food machines: Its growth has been driven by increasing consumer demand for healthy, sustainably produced and fairly traded food. This is because the company, a relative newcomer founded in 2015, is passionate about developing and manufacturing flexible filling machines, designed for the needs of small businesses.
François Junod, Managing Director of EmbaPlan, explains why this market is growing: "Many farmers or other types of producers and even start-ups are marketing their own professionally-filled products, for example yoghurts, juices and fruit preparations. Some of them even make it onto the shelves of regional supermarkets, as more and more consumers are supporting the concept of 'from farm to fork'. We have developed our range of machines for producers who make these kinds of products".
However, for these users, the filling process has to meet some special requirements. Because there are frequent product changes, the machines must be flexible in terms of packaging units and sizes. They should also be capable of filling newly developed products. Naturally, a high standard of hygiene is essential, as are compact design and good cleaning options. And because (almost) every user has their own special requirements and the products to be filled are very diverse, EmbaPlan adapts each individual machine to the particular conditions in each case and also builds fully customized systems.
The range includes the Maximise rotary machines for precision filling of food into cups. François Junod: "These very compact systems can fill liquid or pasty food products. Dosing solids such as fruit or nuts is no problem, and the cup size can be changed in just a few simple steps. Speeds of up to 1,500 cups per hour are possible".
Pneumatics completely reworked, with successful results
The machines were originally built by an external manufacturing service, according to EmbaPlan´s specifications. Later, EmbaPlan decided to build the machines themselves and, in the course of this insourcing, fundamentally overhauled the design.
The pneumatics were one of the areas given special attention. They are of central importance, because almost all essential functions (except for the electrically-driven turntable) are operated by compressed air or vacuum. These functions are cup intake, dosing, filling, lid handling, sealing and discharge of the filled cup.
In selecting the pneumatic components, flexibility was again one of the requirements. For example, depending on the viscosity of the product, dosing it into the cup is done at different speeds. The pneumatic system must be able to handle this, and before the redesign it was, but only to a limited extent.
EmbaPlan approached various suppliers of pneumatic and vacuum system solutions and ultimately decided to work with SMC. François Junod: "We have no expertise in managing pneumatics projects, and our development resources are limited. So, it suited us perfectly when SMC's engineering team made us a basic design proposal."
Base of the new design: the SY valve manifolds
The centrepiece of this basic design is the SY3000/5000/7000 series of valve manifolds. This allows different valve types and sizes to be combined on a single multi-connector panel. Furthermore, thanks to the bus node technology, each valve no longer has to be wired individually, and only two connecting cables are needed to connect the electronics.
This eliminates the need for complex tubing and cable harnesses connecting the pneumatic units. Oliver Trummer, Sales Engineer at SMC: "The bus nodes are a real advantage in every application situation because they make installation easier and faster. There is an additional benefit in the case of food production: the numerous hygiene requirements, from thorough cleaning to washdown processes, are much easier to meet".
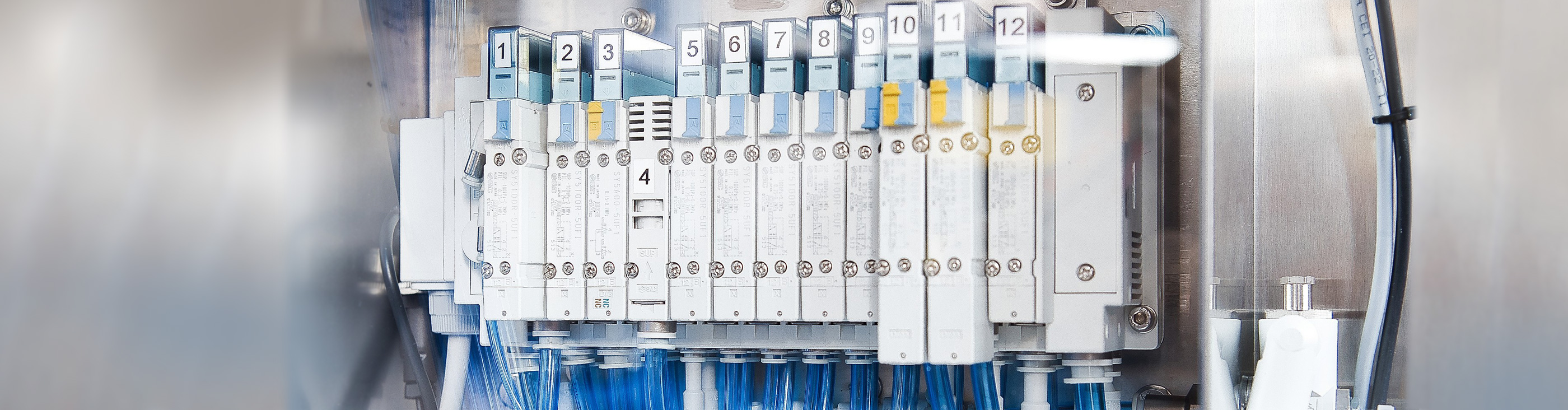
The pneumatics are as flexible as the machine itself
But even more important for EmbaPlan than the compact design, is to be able to quickly and individually adapt the whole pneumatic system to the specific application or customer requirements. This aspect is where the benefits of the SY system really come into play. The Maximize machines are equipped with a valve manifold, housing different types of valve (e.g. 3/2- and 5/2-way valves) in various sizes (SY 3000 and SY 5000), operating at four different pressure levels (including vacuum).
This means that the solenoid valves can be selected individually depending on the machine configuration and the product to be filled, without having to make any alterations to the basic design of the machine. This makes the pneumatics just as flexible as the machine itself. In addition to this, the supply of vacuum or compressed air to any future extension to the installed machines can be easily implemented. Increasing performance is also possible, by swapping over individual valves from the SY3000 to the SY5000 series.
Long service life even with short cycle operation
In spite of their compact size (10 or 15 mm width), the solenoid valves achieve high flow rates, enabling the pneumatic linear drives of the Maximize systems to be controlled in very short cycles. With the short cycles in the packaging process, another real benefit of the solenoid valves with steel slide is their long service life (they are designed for more than 200 million switching cycles), as is their high repeatability, which leads to outstanding process reliability. At the control level, the valve terminal is connected to a Siemens control system.
Valves, actuators, ejectors and accessories from a single source
For EmbaPlan, using actuators from the SMC range was the obvious choice. They mainly use single and double-acting pneumatic cylinders from the C85 and CG5 series, as well as the CRB series of rotary actuators, all naturally in the stainless steel versions, which is normal for food processing machines.
From SMC´s vacuum product portfolio, EmbaPlan uses the ZH series of ejectors among others and, in line with the system concept, also uses the FRL series of maintenance units as well as the hoses and fittings for the pneumatics.
Comprehensive support - flexibility at all levels
The engineers and managers at EmbaPlan are not only very satisfied with the solutions found, but also with the way SMC supported them during the project. François Junod: "We were looking for a partner, not just a supplier. We found one in SMC." As well as the support given in redesigning the pneumatics, it is also about flexibility: Since each machine is configured differently, EmbaPlan orders an individually configured valve manifold each time. So, all participants in the value-added chain are equally flexibile: SMC in customer service, EmbaPlan in the project planning of the filling systems and EmbaPlan customers in meeting market requirements.